Active ingredient batch management enables you to directly process transactions using quantities of active ingredients. Learn about the process and understand the main master data and customizing details that are required to run it.
Key Concept
Base units of measure are the primary units of measure (stock keeping units), but alternative units of measure also can be used to manage specific production, purchase, and sales processes.
Alternative units of measure are directly or indirectly proportional to base units of measure through a maintained conversion in the material master (theoretical conversion factor). Alternative units of measure are useful when alternative units of measure are always convertible through the base units of measure. If the alternative units of measure are not convertible through the base of units of measure and the conversion factor is ever changing, SAP offers a tool called Batch Specific Units of Measure, or Dynamic Alternative Units of Measure. Dynamic Alternative Units of Measure, which are based on real or dynamic conversion factors and not theoretical conversion factors, can manage production, purchase, or sales processes when alternative units of measure could vary or change for every lot that is produced or purchased. Dynamic Alternative Units of Measure can be used as part of the active ingredient batch management process in the materials management (MM), quality management (QM), and Financials (FI) modules.
Active ingredient batch management affects all business processes that involve materials containing one or more concentrates or active ingredients. I explain the main steps to be done in the system by the logistics, quality, and financial departments to perform active ingredient batch management processes in SAP ERP Central Component (SAP ECC) 6.0 with the materials management (MM), quality management (QM), and Financials (FI) modules implemented. I show the main master data and customizing details required for this process. Although I use SAP ECC 6.0 to illustrate this process, it also applies to previous versions.
In addition to the base and alternative units of measure, SAP offers batch-specific units of measure, which are dynamic alternative units of measure not based on theoretical conversion factors, to satisfy the following business requirements:
- Manage business transactions (in purchasing, production, and sales) that are based on not a theoretical conversion factor, but alternative units of measure that could vary or change for every lot that is produced or purchased. Alternative units of measure, which are based on theoretical material master conversion factors, cannot be changed during the execution of the process. That is because material master conversion factors can be changed only as a part of material master data changes. For example, if you are in the juice business, you probably would work with a base unit of each or pieces and an alternative unit with a fixed conversion factor of kg or ton, in which, for example, 1 piece = 100 kg.
- In a batch-specific unit of measure configuration, you define the base units of measure, the corresponding batch-specific units of measure, and the conversion factor that is to be maintained as a characteristic value in the batch received from purchase or production, thus allowing maintenance of a conversion factor for every batch.
- At the point of goods receipt, conversion of quantities maintained in alternative units of measure based on a conversion factor maintained at the batch-characteristics level is called product unit based batch-specific units of measure.
- Similarly, you also can use batch-specific units of measure to calculate the proportions of ingredients with respect to the base units of measure. For example, 100 mL of a particular batch of fruit juice contain 20 mg of vitamin C and 11.5 g of sugar, as well as the fruit juice proportion. This is called proportion-based batch-specific units of measure.
Active Ingredient Management and Business Activities
Active ingredient batch management is supported in the procurement, production, and sales activities involved in batch management, as seen in
Figure 1.
Figure 1
Main activities in the batch management process
In this process, the buying department has the opportunity to create a purchase order (PO) in MM, specifying an appropriate batch, with ingredient management. This feature is also available to the production and sales departments, respectively, using production or process order and sales order management.
I discuss and show in the system the following business activities:
- Maintain active ingredient data for a material
- Create a PO
- Post the goods receipts with reference to the PO
- Display the active ingredient valuation price
- Display the material’s price
- Display the inspection lot
- Conduct quality inspection
- Record the usage decision
- Display the batch master record
- Post the Logistics Invoice Verification (LIV)
- Release the invoice verification
- Check the result in the PO history
Maintain Active Ingredient Data for a Material
To maintain data for a material, you need to update the classification view of the material master AI-1202-01 (a concentrated orange juice that is managed in batch). Follow menu path Logistics > Central Functions > Batch Management > Environment > Material Master > Material > Change > Immediately or use transaction code MM02. Go to the Classification view and make the appropriate entries as shown in
Figure 2.
Figure 2
Active ingredient class defined in the material master’s classification view
Maintain the additional data view for proportion or product units of measure by using transaction code MM02 or following menu path (from the main SAP screen) Logistics > Materials Management > Material Master > Material > Change > Immediately. Go to the Basic Data view and navigate to the Additional Data screen.
In the Additional Data screen, select the Proportion/prod.unit tab, specify the appropriate characteristic, and assign a Plan Value within the allowed range for the characteristic. For the proportion/product unit, enter the value AI01, the new proportion unit in which the active ingredient is measured (
Figure 3).
Figure 3
Link the material to the Characteristic AI01
Define alternative units of measure in the material master’s additional data details. Enter the second line item, as indicated in
Figure 4.
Figure 4
Define alternative units of measure in the material master’s additional data details
Note
In addition to the types of value assignments that are already available, you can assign characteristic values based on the active ingredient quantity and active ingredient price.
You can thus determine the valuation price of a batch using its active ingredient quantity.
Batch management for the material can be activated in the Purchasing view if the involved material is an externally procured material. You can also select batch management in the Plant/Storage Location views used for inventory activities. When you use batch-specific units of measure in purchasing or in production, the planned conversion factor maintained in the material master is used as a default conversion factor.
In the Purchasing view, select the Batch management indicator and populate the Order Unit field with the proportional unit of the batch ingredient. Follow menu path Logistics > Materials Management > Material Master > Material > Display > Display Current or use transaction code MM03. After entering the material code and plant, click the Purchasing tab (
Figure 5).
Figure 5
Define material managed in a batch
In the next screen (
Figure 6) click the Accounting 1 tab and enter X in the Valuation Category field.
Figure 6
Define alternative units of measure in the material master’s additional details
Click the Quality Management tab and maintain the following settings to trigger an automatic inspection lot creation based on a goods receipt against a PO (
Figure 7).
Figure 7
Relevant material master settings for quality management activities
Now you create a master inspection characteristic linked to the Class Characteristic AI01. Use transaction code QS21 or follow menu path Logistics > Quality Management > Quality Planning > Basic Data > Inspection Characteristic > Create (
Figure 8). Create the Master Inspection Characteristic MICAI01 referring to an already existing class characteristic AI01. This characteristic is used to evaluate a batch using the Active Ingredient portion.
Figure 8
Define master inspection characteristics
Now create a material specification. Use transaction code QS61 or follow menu path Logistics > Quality Management > Quality Planning > Inspection Planning > Material Specification > Edit (
Figure 9). Define the upper and lower limits for the actual value of an inspection characteristic.
Figure 9
Define material specifications
Create a standard price for batch-specific units of measure. Use transaction code MWB1 or follow menu path Logistics > Central Functions > Batch Management > Batch-specific Units of Measure > Standard Price > Create. Enter the standard price and price unit (
Figure 10).
Figure 10
Create a proportion or production unit valuation
The batch determination is carried out using active ingredient quantities. The following prerequisites need to be met:
- You have entered the underlying transaction in active ingredient quantities.
- You have set the indicator Display Unit of Measure as a unit of entry in the strategy record. Do this in customizing. Follow menu path Logistics – General > Batch Management > Batch Determination and Batch Check > Strategy Types > Define Process Order Strategy Types (Figure 11).
- You need to use the standard MM transactions to perform the purchasing cycle for active ingredient management materials. An active ingredient proportion always differs from the actual value of the batch.
Figure 11
Set the indicator Display Unit of Measure as a unit of entry in the strategy record
Note
Planning, materials planning, and availability checks are carried out in physical quantities. You can use an inventory correction factor to determine the active ingredient quantity actually available in stock in the Available-to-Promise (ATP) availability check and in requirements planning. You can find this function in the material master by following menu path Batch > Active ingredient management > Inventory corr. factor (report RVBWSCOR).
A correction factor is useful if the following scenarios arise:
- The material contains only one active ingredient.
- The material contains several active ingredients, but only one active ingredient is relevant for the availability check.
Create a Purchase Order
Because you can store the PO either in physical quantities (base units of measure) or in active ingredient quantities, enter active ingredient quantities and active ingredient proportion units as PO quantities and order units, respectively. If POs are made in active ingredient quantities, the PO quantity and physical quantity are updated in the PO history. In this way, the degree of PO fulfilment can be determined at any time in active ingredient quantities. All fulfilments are checked against the PO quantity.
To create a PO for the material AI-1201-001 that contains an active ingredient measured in the proportion unit I01, use transaction code ME21N or follow menu path Logistics > Materials Management > Purchasing > Purchase Order >Create > Vendor/Supplying Plant Known (
Figure 12).
Figure 12
Create a PO for Active Ingredient Management materials
The quantity of active ingredient that is actually delivered may differ slightly from the quantity ordered. Therefore, you need to maintain the tolerances accordingly in the line-item Delivery tab. If needed, specify these details in the Overdelivery and Underdelivery fields as indicated in the
Figure 12.
Post the Goods Receipts with Reference to the PO
The warehouse department can post the goods receipt for the PO in base units of measure either by using transaction code MIGO or by following menu path Logistics > Materials Management > Inventory Management > Goods Movement > Goods Receipt (MIGO) (
Figure 13).
Figure 13
Perform goods receipt with reference to the PO
The base unit of measure for material AI-1201-001 is kg. Only the physical quantity can be determined in goods receipt. In this case, 100 kg are delivered. If the active ingredient proportion of the batch is not known at the time of goods receipt, the goods receipt is carried out according to the planned proportion. If the actual proportion is taken from the usage decision in QM, the PO can be subsequently debited.
The planned value is used first to calculate the active ingredient content when a goods receipt posting is made in the base unit of measure. In this case, the planned value in the material master for the proportion unit I01 is 50 percent. Therefore, the system first assumes a delivery of 50 I01 was made.
Enter a batch number of your choice or accept a number assigned manually. Do not valuate the characteristic active ingredient. You can also display values in proportion units. You can find this function by choosing Goto > Additional functions > Quantity conversion.
To display the PO history, use transaction code ME23N or follow menu path Logistics > Materials Management > Purchasing > Purchase Order > Display. On the Item Detail screen, select the tab Purchase Order History. The system displays the goods receipt (
Figure 14). The system first assumes that the ordered quantity was delivered (50 I01).
Figure 14
Display the PO history
Display the Active Ingredient Valuation Price
Because the active ingredient of material AI-1201-001 has its own valuation price, you need to display its valuation record to check that the price for the active ingredient has been updated based on the latest good receipts performed in the system. Use transaction code MWB3 or follow menu path Logistics > Central Functions > Batch Management > Batch-Specific Units of Measurement > Standard Price > Display (
Figure 15).
Figure 15
Display the active ingredient valuation price
Display the Material’s Price
To check that the price of the ingredient management has been updated based on the latest good receipt performed in the system, you can display the average price, standard price, and total stock of the active ingredient material in the Financial Accounting view, in which the valuation type represents the batch level. Use transaction code MM03 or follow menu path Logistics > Central Functions > Batch Management > Environment > Material Master > Material > Display Current. The system displays the price per base units of measure. This price is based on the assumption that the base units of measure contain the same active ingredient proportion as specified in the planned value (
Figure 16).
Figure 16
Display the new valuation price in the Accounting 1 view
Display the Inspection Lot
Upon goods receipt, the system automatically creates an inspection lot. To display the inspection lot (to ensure, for example, that the settings for the QM module have been done appropriately), use transaction code MIGO, specify the material document, and then click the InspLot button, as indicated in
Figure 17.
Figure 17
Display the material document and associated Inspection Lot
Figure 17 Display the material document and associated Inspection Lot
The main details of the inspection lot are reported in the screen shown in
Figure 18. The quality management department should process this inspection lot to ensure the materials are available for further use. To get to the screen in
Figure 18, click the InspLot button in
Figure 17.
(Alternatively, you can use transaction QA03 or following the menu path Logistics > Quality Management > Quality Inspection > Inspection Lot > Processing > Display).
Figure 18
Display the inspection lot
Conduct a Quality Inspection
The goods receipt for material AI-1201-001 appears in quality inspection. You should have just measured the potency of the active ingredient. To enter the inspection result, use transaction code QE51N or follow menu path Logistics > Central Functions > Batch Management > Environment > Quality Inspection > Worklist > Results Recording (
Figure 19). Select the inspection lots for your material. In the Result field in the data entry section, enter the actual inspected value. (The actual values are usually different from the planned values.) Press Enter to confirm. Save your data.
Figure 19
Record results upon the inspection
Record the Usage Decision
To record the usage decision, use transaction code QE51N or follow menu path Logistics > Central Functions > Batch Management > Environment > Quality Inspection > Worklist > Results Recording (
Figure 20). Double-click the line with your inspection lot in the work list. In the UD code field, use F4 help to enter an acceptance without further action (code A) and save the usage decision.
Figure 20
Record the usage decision (accept the inspection)
In this case, the whole goods receipt quantity (100 kg) is to be posted into unrestricted stock, as shown in
Figure 21.
Figure 21
Record the usage decision (all goods in unrestricted status)
During the recording of the usage decision, the system provided the following message:
Correct purchase order history for inspection lot using transaction MWBQ. In this step, update the PO history with transaction code MWBQ, as shown in
Figures 22 to
24.
Use transaction code MWBQ or follow menu path Logistics > Central Functions > Batch Management > Batch-specific Units of Measure > Subsequent Adjustment f. Goods Receipt > Enter with Ref. to Insp. Lot. In the screen that appears (
Figure 22), enter the inspection lot number, the document date, and posting dates. Click the execute icon.
Figure 22
Update the purchase order history based on the inspection lot results
After you save the adjustments shown in
Figure 23, you receive the status message shown in
Figure 24.
Figure 23
Display and save the adjustments proposed
Figure 24
Information message received by SAP upon saving
To display the updated PO history, use transaction code ME23N or follow menu path Logistics > Materials Management > Purchasing > Purchase Order > Display. On the Item Detail sub-screen, select the Purchase Order History tab (
Figure 25). The system displays the goods receipt. The system first assumes that the ordered quantity was delivered (50 I01).
Figure 25
Display the PO history
Display the Batch Master Record
The characteristics of the batch were valuated in the inspection process with the inspection result from the QM. To display the batch classification, use transaction code MSC3N or follow menu path Logistics > Central Functions > Batch Management > Batch > Display and select the Classification tab.
The result from QM has been transferred. The batch has a value that differs from the planned value for the active ingredient characteristic, as shown in
Figure 26. Verify that the active ingredient quantity of the batch has been updated.
Figure 26
Display the batch master (Active Ingredient value) to verify that the active ingredient quantity of the batch has been updated
Post the Logistic Invoice Verification
To post the Logistic Invoice Verification (LIV), use transaction code MIRO or follow menu path Logistics > Materials Management > Logistics Invoice Verification > Document Entry > Enter Invoice. Click the Basic Data tab and enter data for the PO document number, invoice date, reference, amount, and tax data as shown in
Figure 27.
Figure 27
The LIV screen
Note that the system accepts the invoice even though the amount specified is higher than planned. This is because of the over-delivery that was posted for the PO. The over-delivery was possible because a tolerance was entered for the PO item.
The system responds with a warning message (
Figure 28).
Figure 28
Warning message provided by the system upon invoice processing
Release the Invoice Verification
To release the LIV so that it can be paid to the vendor, use transaction code MRBR or follow menu path Logistics > Materials Management > Logistics Invoice Verification > Document Entry > Enter Invoice. Enter the invoice document number and then run the report. The system shows the details reported in
Figure 29. The user then selects the line item and clicks the flag icon to release the LIV.
Figure 29
Release the invoice verification
Check the Result in the PO History
To display the PO history, use transaction code ME23N or follow menu path Logistics > Materials Management > Purchasing > Purchase Order > Display. On the Item Detail sub-screen, select the Purchase Order History tab.
The system displays the goods receipt (
Figure 30). The system assumes that the ordered quantity was delivered (50 I01). Verify that the LIV document has been reported on the PO history tab.
Figure 30
Display the PO history
Customizing Activities
Now I list the most important customizing settings that are necessary to implement the batch ingredient management solution in procurement.
Step 1. Activate batch-specific units of measure. First, activate ingredient management functionality at the client level. Use transaction code OMWS or follow menu path Tools > Customizing > IMG > Edit Project (SPRO). Click the SAP Reference IMG button. In the main customizing screen follow menu path Logistics – General > Batch Management > Batch-Specific Material Units of Measure > Activate Batch-Specific Material Units of Measure.
Note that you need to select the Active radio button to ensure that batch management is active (
Figure 31).
Figure 31
Activate the batch-specific units of measure
Step 2. Create units of measure for proportion unit. To run batch-specific units of measure, a characteristic is required to be added to the batch class that carries the conversion factor for deriving the alternative batch-specific unit of measure. Therefore, you must create this unit of measure before proceeding. If this unit of measure already exists in the system, then continue to the next step.
Create the non-dimensional unit of measure that is used as a unit of measure for the characteristics. Use transaction code CUNI. To create a unit of measure for your active ingredient that should act as a proportion unit of measure, follow customizing menu path Tools > Customizing > IMG > Edit Project (SPRO). Now follow menu path SAP NetWeaver > General Settings > Check Units of Measurement. Click the Units of Measurement (no dimensions) button. In the screen that appears, enter transaction code CUNI and click the create icon

. In the next screen (
Figure 32) enter the details for the unit of measure for your active ingredient that should act as a proportion unit of measure.
Figure 32
Details of units of measure for proportional unit
Step 3. Create units of measure for the ratio unit. Create another unit of measure (non-dimensional) for the ratio between the physical quantity and the active ingredient quantity. Follow menu path Tools > Customizing > IMG > Edit Project (SPRO). Click the SAP Reference IMG button. Now follow menu path SAP NetWeaver > General Settings > Check Units of Measurement. Click the Units of Measurement (no dimensions) button. In the next screen choose Create. The next screen that appears (Figure 33) includes the details of the unit of measure for the ratio unit.
Figure 33
Details of the unit of measure for the ratio unit
Step 4. Define the proportion unit. Assign the units of measure from the role of proportion units of measure (Figure 32). Enter the units of measure in the table of the batch-specific material units of measure. Search for an appropriate reference unit of measure with the dimension mass. Follow menu path Tools > Customizing > IMG > Edit Project (SPRO). Click the SAP Reference IMG button. Now follow menu path Logistics – General > Batch Management > Batch-Specific Material Units of Measure > Edit Batch-Specific Material Units of measure. You also can use transaction code BMA1.
Make a new entry for the unit of measure I01. It should be able to be used as a batch-specific unit of measure. Enter the dimension Mass as the reference unit of measure (
Figure 34).
Figure 34
Define the proportion of the unit of measure for the proportional unit
Step 5. Define a ratio unit of measure (i.e., calculate the proportion unit from the base unit).
First, define the relationship between the active ingredient (proportion unit) and the physical quantity for the units of measure. Use the proportion unit and the base units of measure KG defined in
Figure 34. This data helps the system convert from the base units of measure to batch-specific units of measure.
Similarly, you also can configure the conversion of batch-specific units of measure to base units of measure. Follow menu path Tools > Customizing > IMG > Edit Project (SPRO). Click the SAP Reference IMG button. Now follow menu path Logistics – General > Batch Management > Batch-Specific Material Units of Measure > Calculate Proportional Factors > Define Calculation of Proportion Quantity from Base Quantity or use transaction code BMA3. Choose New Entries. Enter the commercial format, batch-specific units of measure, and base unit of measure information, as shown in
Figure 35.
Figure 35
Define the ratio unit of measure
Step 6. Create the conversion factor characteristics for the batch class. Use transaction code CT04 and assign the same to the batch class of the product that requires the batch-specific conversion. Assign the unit of measure created in step 3 – Batch Specific conversion factor unit of measure (
Figure 33). For example, you can create characteristics called AI01 with a description Active Ingredient with unit of measure U01.
The characteristic that you create needs to be in a numeric format and it cannot carry multiple values. All the data you need to define for this characteristic is defined in
Figures 36,
37, and
38. Enter the values as listed in
Figures 36 and
38 and specify the appropriate characteristic values in
Figure 37. Define the basic data for the characteristic AI01,
Figure 36.
Figure 36
Define main data for the characteristic
Define the appropriate value range for the characteristic’s values (Figure 37).
Figure 37
Define a characteristic’s value range
Assign class type 022 and 023 to the characteristic AI01 (
Figure 38).
Figure 38
Assign a class type to a characteristic
Step 7. Assign the conversion factor characteristics to batch class. Use transaction code CL02 and assign the characteristics (conversion factor characteristics) to the batch class, as shown in
Figures 39 and
40.
Figure 39
General data of the class
Figure 40
Assign a characteristic to the class
In addition to assigning the characteristics to the class, you also must classify the batch class at the header as a Special Batch Class by entering a value S (Substance Steel) in the class header of the field Organizational Area (
Figure 39). You also include the value S for the characteristics in the screen in which you list the characteristics of the class (the Characteristics tab of the Class Change transaction) as shown in
Figure 40. This step ensures that the system uses this characteristic in carrying out the batch-specific units of measure functionality.
Note
This batch class should be assigned to the material master, which requires the functionality of batch-specific unit of measure. For example, you can assign the characteristics AI01 to the class AICL01 and then assign this batch class to the material AI-1202-01.
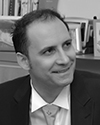
Gaetano Altavilla
Dr. Gaetano Altavilla is a senior SAP practice manager. His focus is on pre-sales, delivery of SAP application solutions for large international corporations, and SAP knowledge management in Europe, the Middle East, and Africa (EMEA).
In his 18 years of SAP application experience working for many multinational companies, such as Procter & Gamble and Hewlett-Packard, he has covered a wide range of ERP logistic areas, focusing on the MM, WM, SD, LES, PP, PP-PI, PLM (QM, PM, PS) modules, as welll as CRM (TFM), SRM (EBP), SCM (SAP APO), and MES (ME) components.
Dr. Altavilla holds a degree with first-class honors in mathematics from the University of Naples and is certified in many SAP modules: SAP Logistics Bootcamp, SAP MM, SD, LE (SHP/WM/LE), PP, PLM (PM, QM, PS), SRM, CRM, SCM (APO), SCM (TM), FI, CO, and Solution Manager. He also has experience in ABAP/4 and application link enabling (ALE) and IDocs. He has participated in numerous industry conferences, such as the SAP Skills Conference in Walldorf at SAP SE.
You may contact the author at
Gaetano_altavilla@hotmail.com.
If you have comments about this article or publication, or would like to submit an article idea, please contact the
editor.