Learn about the new Global Available-to-Promise (Global ATP) functionalities introduced in SAP SCM 5.0 to meet your company’s delivery planning demands. Get a sneak preview of improved Global ATP functionalities available in SAP SCM 2007.
Key Concept
The new Global Available-to-Promise (Global ATP) functionalities in SAP SCM 5.0 help companies align their sales and delivery processes with the full logistics picture. Global ATP integrates SAP’s technology with your company’s stock levels, production capacities, and global market commitments. SAP Advanced Planning and Optimization’s Global ATP is an extension of the ATP feature in R/3 and is designed for more complex or demanding business scenarios. The Global ATP advanced tools discussed in this article include rules-based ATP with alternative product and location information, Capable-to-Promise based on finite scheduling production, flexible product allocation, and an improved backorder processing tool.
SCM 5.0 and SCM 2007 provide major improvements in Global Available-to-Promise (Global ATP) functionality. In this third part of my series on SCM 5.0, I’ll walk you though four main advancements in SCM 5.0, including rules-based ATP (RBA), Capable-to-Promise (CTP), backorder processing (BOP), and the integration of SAP CRM and Global ATP. Throughout each section, I highlight further improvements coming with SCM 2007. I’ll also show you how to check the ATP settings and instructions in SCM 5.0 and SCM 2007.
In part 1 of my SCM 5.0 series, I introduced the benefits of new developments in Demand Planning (DP), Supply Network Planning (SNP), and Capable-to-Match (CTM). Part 2 described the new developments in Production Planning and Detailed Scheduling (PP/DS) and Demand Planning (DP) offered in SCM 5.0. In the previous articles, I described two functionalities related to Global ATP in SCM 5.0, including:
- You can use the interchangeability of master data to drive rules-based ATP
- You can integrate transportation constraints, driven by Transportation Planning and Vehicle Scheduling (TP/VS), with ATP so that the system checks an item’s availability and delivery route simultaneously
Check Instructions Settings
To maintain check instructions, follow IMG menu path APO>Global ATP>General Settings>Maintain Check Instructions. Based on sales order parameters, the check instructions options define the sequence and settings that trigger ATP processes. These settings drive the corresponding processes. Figure 1 compares the differences in check instructions settings between SCM 4.1 and SCM 5.0. Specifically, new settings related to rounding and third-party scenarios are added in SCM 5.0, such as the rounding procedure and third-party order processing.
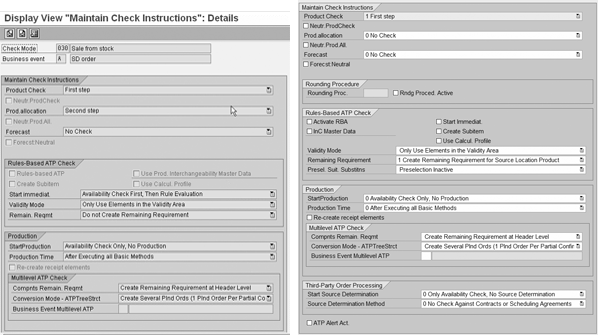
Figure 1
Comparison of the Maintain Check Instructions screen in SCM 4.1 on the left and SCM 5.0 on the right
SCM 2007 offers a new setting, Type of PAC (product availability check), which enables your system to set only fixed pegging relationships in the ATP checking process, for example. Pegging is a production concept that refers to the relationship generated between different procurement and demand elements that are planned or created after the levels of a bill of material (BOM). You can control how or if the fixed pegging should be considered, as shown in Figure 2. Fixed pegging establishes a link between a procurement and demand element in a specified location. For a detailed explanation on pegging, refer to my quick tip article, “Demystify the Pegging Concept,” in this update.
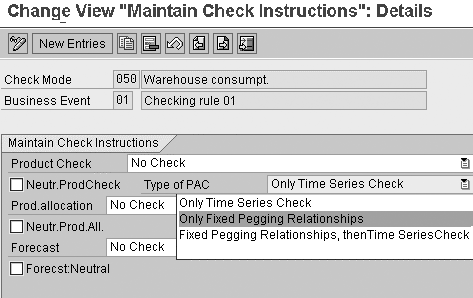
Figure 2
SCM 2007 offers three new product availability check options
New Global ATP Functionality
One of the most improved areas in SCM 5.0 is the Global ATP functionality. Global ATP is further equipped to meet your company’s increasingly complex, global demands. I’ll introduce four common scenarios supported by Global ATP and describe how you can take advantage of your SCM 5.0 technology right away. I’ll describe the following scenarios:
- RBA
- CTP
- BOP
- New Global ATP scenarios integrated with SAP CRM 2005
RBA
During the ATP check, RBA functionality offers alternative products or alternative delivery locations to the customer when a required item or location is not available. RBA offers several beneficial functionalities, such as Multi- Item Single Delivery Location (MISL), location restriction, and consolidation location with stock transfer orders.
MISL
MISL, also known as the complete delivery functionality, verifies if all items in the sales order are available in a single location. The main benefit of MISL is reduced transportation costs, because sales orders are delivered from a single location. If you are familiar with creating a sales order (transaction VA01 in R/3 and SAP ERP Central Component [ECC] 5.0), then you’ve probably seen the Complete dlv. (complete delivery) option. Selecting this option allows you to consolidate all items in a sales order into a single delivery (Figure 3).
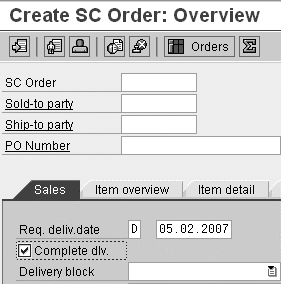
Figure 3
The complete delivery option in a sales order
Companies that require complete or full-load deliveries from a single location, due to cost factors such as full truck load requirements, may find MISL particularly useful. When the sales order processing system (R/3 or SAP CRM, for example) triggers an ATP check, MISL determines whether all items requested in the sales order are available in a single location. The system tries each location until it finds one. If a single location is not found, the items remain partially confirmed or unconfirmed. New Global ATP flexibility in SCM 2007 addresses this situation. Rechecking the availability of multiple items in several locations at the sales order level is not possible in earlier releases. All SCM releases prior to 5.0 could only perform ATP checks on one item at a time.
In the next example, the complete delivery option is selected and a four-step location substitution rule is defined as 3100?3300?3400?3700. This specific rule is a sorted list of locations, which means the system checks location availability in location 3100 first, and then tries 3300, and so on. Substitution rules are APO master data that you can define by following menu path APO>Master Data>Rule Maintenance>Integrated Rule Maintenance or by executing
transaction /SAPAPO/RBA04.
Your system recognizes this rule and searches for which location can deliver all of the items (e.g., products MISL-P1, MISL-P2, and MISL-P3). APO’s availability check results are shown in Figure 4. The green lights in the Rqmt Quantity column indicate that location 3700 confirms availability of all items for delivery. It means that the sales order with an initially desired source at plant 3400 can be fully confirmed and delivered from plant 3700 only. According to the ATP results, the system automatically updates the location in the sales order by creating an additional item that shows where the order is confirmed.
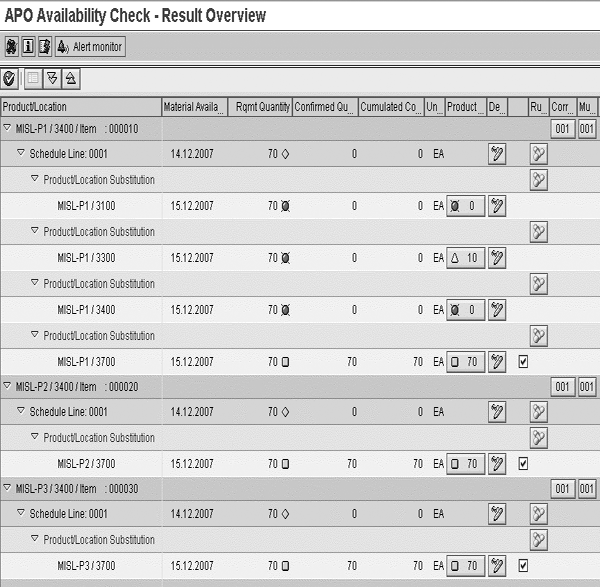
Figure 4
APO availability check results with the complete delivery option selected
The Rqmt Quantity column represents the required quantity and the Product (product availability) column reflects the quantity available in a location. For example, location 3300 in Figure 4 has 10 units available in the Product column, but cannot confirm the sales order because it doesn’t have the full amount (70 units) available in that location.
SCM 2007 offers additional MISL functionality that helps you overcome scenarios in which all items are not available in one of the checked locations. Three different solutions are available:
1. Generate remaining requirements for the input product in the first substitute location. For example, if a sales order asks for 20 units and the ATP process confirms only five units, this option allows you to decide where to create the requirement for the remaining 15 units.
2. Generate the remaining requirements for the first substitute product in the first substitute location
3. Generate the remaining requirements for the last substitute product in the first substitute location
Location Restriction
Another RBA feature in SCM 5.0 is location restriction. This functionality is an enhancement to the rules maintenance screen, which you access by executing transaction /SAPAPO/RBA04. You can restrict the maximum number of locations during location substitution. Location restriction is especially useful if you define only one location substitution to avoid long distribution routes, for example. In addition, you can adapt the substitution rules to consider new or temporarily closed locations. This option is not possible in SCM releases prior to 5.0. The only way to remove a new or closed location from your results is to manually delete the location from the rule.
Consolidation Location with Stock Transfer Orders
Consolidation location is another RBA feature in SCM 5.0. This functionality is useful when a customer requires a delivery from a specific consolidation location or if you want items from different locations to be delivered to one location and further consolidated into a single delivery, such as in the export business.
Figure 5 illustrates how stock transfer orders are created between sourcing and consolidation locations. In this scenario, the system checks the consolidation location first and if delivery is not possible, then it follows the substitution rules and searches for the material availability.

Figure 5
The consolidation process during an ATP check creates stock transfer orders
CTP
This feature is commonly used by companies with complex products that contain many characteristics. For example, steel manufacturers deal with thousands of characteristics and may use CTP because every sales order is different. CTP may be considered the most sophisticated ATP method because it is mainly based on PP/DS capabilities. CTP integrates PP/DS and Global ATP to provide information that takes into account production capacity and product or component availability. For example, the system checks if a sales order can be delivered on time, based on the current load your work centers allow. If the delivery cannot be on time, then your system automatically determines when it may be feasible.
In every new APO release, CTP continues to improve dramatically. New features and enhancements in SCM 5.0 and 2007 are partially attributed to the advances in PP/DS functionality. For example, in SCM 5.0, you do not need to create a new planned order or other procurement element to adjust minor quantity changes in a sales order for make-to- order
items. Instead, your system uses the underdelivery tolerance option to solve this scenario.
As of SCM 5.0, when the quantity of a sales order item (that was previously confirmed) is reduced within the defined tolerance, the system doesn’t create additional procurement elements to cover the originated gap. To model this scenario, select the Underdel. Tol. indicator in the APO product master data under the Lot Size tab (Figure 6). Now, underdelivery tolerance is introduced in the sales order item as part of the shipping information.
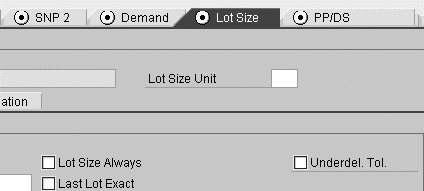
Figure 6
New underdelivery tolerance option in APO’s product master data
One significant PP/DS improvement in SCM 2007 that helps CTP functionality is the capacity reservations feature. To generate the screen shown in Figure 7, follow menu path APO>Master Data> Resource and click on the Capacity Reservation button, which is located in the PP/DS BucketCap tab. Users can reserve critical resources for their most important customers.

Figure 7
SCM 2007 capacity reservations for a resource
For example, 168 units (hours) of this resource are allocated for a particular customer (indicated by the KUNNR characteristic) and the order is scheduled to process if capacity is available on those intervals with reserved hours. Specify the capacity reservation in the Collective Allocation column. The Res. Rel. Date column indicates the date when this reservation ceases to exist. The capacity reservations feature is very important for industries that are required by sales contract obligations to reserve resources in advance for their top customers.
A second functionality added in SCM 2007 is a new interactive heuristic feature that you manually trigger to execute a CTP check for a sales order. Now the planner corrects the resource capability or any missing parts to generate a new date for the sales order. After the sales order is accepted by the user, BOP is automatically executed and updates the sales order with the newly confirmed date and quantity. Although this article only describes a few CTP enhancements, several other PP/DS improvements are available to create more efficient CTP results and cover different business scenarios.
BOP
BOP is the main tool to align the ATP situation with both the logistics picture (e.g., stock data and purchase orders) and the sales order data (e.g., priority and required dates), in your SAP system. During the BOP process, the system checks if the originally confirmed sales order should be reconfirmed or unconfirmed, to accommodate more or less important sales orders.
BOP usually occurs overnight and generates a log report of confirmed and unconfirmed orders. Each morning, the user (usually a sales analyst) revises the report and either confirms or rejects the results. However, you may be wondering what happens between two BOP executions. The answer is Event-Driven Quantity Assignment (EDQA), which is especially important for companies with a large amount of transactions or sales orders.
EDQA, a new SCM 5.0 process, improves BOP by allowing the system to react immediately to events affecting the stock availability, such as changes in documents (e.g., sales and purchase orders) or in stock data. For example, you could use an unexpected goods receipt to confirm a high-priority sales order. When the system initially executes BOP, the system does not confirm the sales order because it does not show enough available products to fulfill the sales order.
When the ship-to party receives the order and it is registered in the system, the receipt quantity can fulfill some sales orders that BOP could not confirm. The system automatically triggers EDQA when a determined event occurs and corrects the sales order confirmation. For example, if the system confirmed a low-priority sales order previously, EDQA considers the goods receipt and can instead confirm a higher-priority sales order in the order due list (ODL) of the same product. The ODL is how the system filters and sorts sales orders according to business priority
EDQA allows you to correct inappropriate product assignments that sometimes occur between two BOP executions. Figure 8 shows the workflow tasks that EDQA triggers to react to certain events, such as a goods receipt. The confirmation process triggered by EDQA is based on the ODL. ODL is a list that contains both confirmed low-priority sales orders and unconfirmed high-priority sales orders.

Figure 8
Workflow tasks triggered by the EDQA functionality to adjust the sales order’s ATP
To maintain the ODL manually, use the new SCM 5.0 transaction /n/SAPAPO/ODL or follow menu path APO>GATP> EDQA>Process Order Due List. ODL settings allow you to define which sales orders are considered high or low priority by either adding or removing items or manually assigning priority to a specific sales order.
Based on the settings you select, the system confirms the higher priority sales orders and removes the confirmations from the lowest priority ones, if required. As shown in Figure 8, EDQA involves workflow definition tasks and other customizing activities that allow you to react to events based on your business requirements. Access EDQL settings and ODL customizing activities by following IMG menu path APO>Global ATP>Event-Driven Quantity Assignment.
Ensuring that BOP is performing properly is essential for scenarios with a slim execution window. SCM 5.0 alleviates potential performance headaches with new BOP parallelization functionality. Parallelization enables your system to run BOP activities (such as filtering, preparing, checking, and updating) in a parallel mode, which reduces the total execution time. Sorting activities are executed sequentially because all items are included in this BOP activity.
Instead of executing BOP for all items at the same time, SCM 2007 introduces the item bundle functionality. This option groups items on a minimum/maximum basis and is especially advantageous because you can parallelize the process as orders are grouped. Additionally, variant splitting can be used to parallelize BOP. Both the item bundle and variant splitting functionality in SCM 2007 lead to more efficient BOP performance, which is a fairly time-consuming task in earlier SCM system versions.
Integration with SAP CRM
Integrating your ATP processes with SAP CRM is an initiative among companies to improve order management. Perhaps your company requires a more sophisticated sales order management system for your call center or internet sales, but also needs ATP processes readily available. New integration scenarios are introduced, including kit to order, special dynamic safety stock, rounding, or third-party availability check.
Note
For tips on Sales and Distribution (SD) functionality available in CRM, including Global ATP, read Karen Lindholm’s article “
New SD Plant Functionality in CRM 2005 available in the SCM hub of SAPexperts.
Kit to Order
Kit to order provides a way to check the availability of a set of items (kit) or a BOM’s exploded components, in which the quantity of the components is calculated based on master data. From a logistical standpoint, all items in a kit are processed collectively, during picking and packing stages, for example. Your SCM system uses the kit’s BOM to run an availability check on individual kit components. For this task, RBA can be used to find alternative components.
Packing or transportation restrictions usually require confirmed quantities to be packed or shipped in specific bulk units, such as a full pallet. To meet these requirements, SCM 5.0 contains a new rounding functionality, which allows Global ATP to round confirmed quantities. In this way, if the customer asks for 30 boxes in 10 box pallets, and you can confirm only 16 boxes, then the system proposes to deliver one pallet (which is 10 boxes).
To activate this functionality, execute transaction /SAPAPO/AC12. You can specify different parameters, such as package size per location or rounding direction (e.g., up, down, or to the nearest) to control the results.
Special Dynamic Safety Stock
Rounding or Third-Party Order Processing
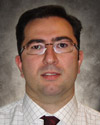
Adolfo Menéndez Fernández
Adolfo Menéndez Fernández is the application architecture manager at Repsol in Madrid. Previously, he worked at SAP Consulting Spain as the logistics consulting manager. He studied at the University of Oviedo, where he earned an electronic engineering degree. He is a certified SAP consultant in supply and demand planning (SNP and DP), order fulfillment (Global Available-to-Promise), production planning and detailed scheduling (PP/DS), as well as procurement and materials management (MM). Adolfo has more than 10 years of SAP implementation experience in the consumer product goods, pharmaceutical, automotive, furniture, textile, chemical, oil & gas, and steel industries using SAP ERP logistic modules (including PP, MM, and sales and distribution [SD]) as well as SAP SCM (DP, SNP, and PP/DS). He is APICS certified in Production and Inventory Management (CPIM).
You may contact the author at asturiasadolfo@yahoo.com.
If you have comments about this article or publication, or would like to submit an article idea, please contact the editor.