See how a manufacturing company created a new third-party logistics (3PL) code to represent a third-party logistics service provider. By incorporating 3PL into supply chain planning, the manufacturing company could plan against changing demand and supply position at 3PL and replenish the 3PL site to achieve the desired customer service level.
Key Concept
A purchase information record is a master data record in an SAP system that establishes the relationship between material code and the supplying vendor. A special procurement key is a master data record in an SAP system that establishes the link between two plants or two distribution centers for stock transfer processing between the linked locations.
The pharmaceutical industry has become extremely competitive due to the rise of the generic drug market. This market also has become complex due to global supply chains. The rising costs of research and development and the declining profit margin of generic drugs makers have led some specialty branded drug-making companies to improve their bottom line by looking at opportunities to optimize their operational costs. One such opportunity is to outsource noncore supply chain operations such as the in-house distribution center to third parties. However, outsourcing of in-house distribution center (IHDC) operations to a third-party logistics (3PL) service provider requires a design change in ERP and SCM systems. The change can vary in each case as the system landscapes of companies vary.
I describe a scenario in which, because of a design and business requirement, a new code 3PL was created to represent a third-party logistics service provider. The existing code IHDC, representing the in-house distribution center, was removed from planning in the manufacturer’s ERP system. The code 3PL in the manufacturer’s ERP system represented all operational transactions, such as sales order, purchase order, and inventory movements, at the third-party logistics service provider’s warehouse. The third party’s ERP system was integrated with the manufacturer’s ERP system via electronic data interchange (EDI) to send and receive the transactional data (Figure 1).
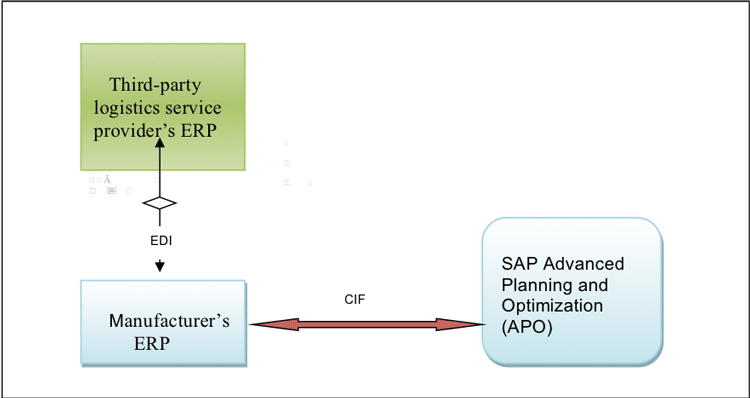
Figure 1
The integrated system landscape
Note
From an SAP Advanced Planning and Optimization (APO) perspective, the new 3PL code replaced the old IHDC code in the complex supply networks and was integrated in APO using the core interface (CIF). In this document, APO screenprints of one supply chain (from the North America supply site NA to the Canadian national IHDC) are provided for understanding. To imagine the complexity, master data is also provided for two other supply chains where the supply site is in Asia/Pacific and in the Europe, Middle East, and Africa (EMEA) regions supplying into the Canadian national IHDC.
The business process to close in-house distribution center operations and go live with the third-party logistics service provider spanned a period of approximately two months from October to December. During this period, all the customer sales orders that were already received were to be shipped out of the in-house distribution center, and excess stock was transferred from IHDC to 3PL. Considering the lead time for completion of the stock transfer, stock was in transit status until the stock was received into the 3PL. In effect, during the cutover period, inventory and receipts were available at two locations for a given product. During the cutover, the manufacturer faced the following business challenges:
- The upstream supply sites’ production plans should not be disrupted and should get a demand signal after netting stock or stock in transit considering both the locations IHDC and 3PL.
- The ability to deploy stock on hand or receipts for forward visibility and dispatch the shipment of available stock into 3PL as well as IHDC. Figure 2 shows various deployment scenarios based on supply site and replenishment lead time. The constraint is that stock and receipts within replenishment lead time can’t be deployed into IHDC and therefore should be deployed into 3PL.
- Transfer stock from IHDC to 3PL without the loss of sales or stockouts during the cutover period.

Figure 2
Deployment scenarios based on supply site and replenishment lead time
Abbreviations Used in the Document
Code
|
Description |
APAC |
Supply plant in the Asia/Pacific region |
NA (B02_1402) |
Supply plant in North America |
EMEA |
Supply plant in the EMEA region |
IHDC (B02_7301) |
Canada in-house national distribution center |
3PL (B02_7303) |
Canada third-party service provider |
RWH1 |
Canada regional warehouse |
RWH2 |
Canada regional warehouse |
RWH3 |
Canada regional warehouse |
P001 and P002 |
Unique product code supplied by APAC and EMEA, respectively |
PIR |
Purchase information record |
SPK |
Special procurement key |
Table 1
Code and abbreviations
Figure 3 is a diagram of the supply chain network created using a purchase information record (PIR) and special procurement keys (SPKs).
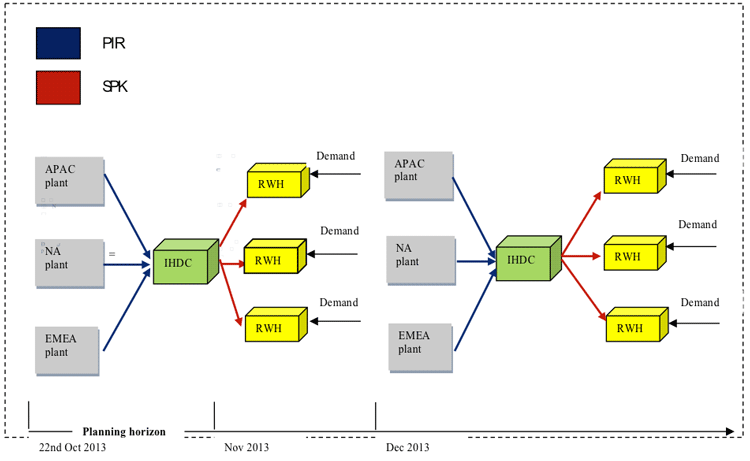
Figure 3
A supply chain network created from a PIR and SPKs
The supply chain network shown in Figure 3 was created using the transportation lane setup shown in Table 2.
From location
|
To location
|
Valid start date
|
Valid end date |
Master data
|
Description
|
APAC
|
IHDC |
01/01/1990 |
31/12/9999
|
PIR1 |
PIR |
NA |
IHDC
|
01/01/1990 |
31/12/9999 |
5300035007
|
PIR |
EMEA |
IHDC |
01/01/1990 |
31/12/9999 |
PIR3 |
PIR |
IHDC |
RWH_01 |
NA |
NA |
SPK1 |
SPK |
IHDC |
RWH_02 |
NA |
NA |
SPK2 |
SPK |
IHDC |
RWH_03 |
NA |
NA |
SPK3 |
SPK |
Table 2
An example of a transportation lane setup
Figure 4 shows how a transportation lane can be displayed using transaction code /n/sapapo/tl1. In my example I specify the Model Name as 000, the Start Location as B02_1402 (the NA supply site), and the Dest Location (destination) as B02_7301 (the IHDC customer location). After entering these values, click the Display button.
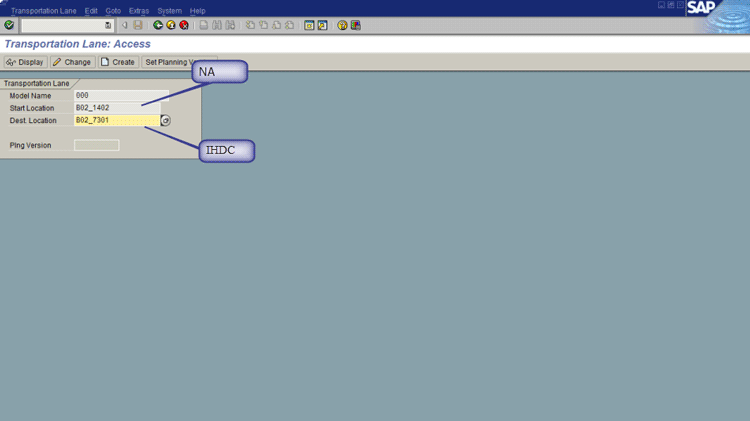
Figure 4
Display a transportation lane
Figure 5 shows the details of the transportation lane created after integrating a PIR from SAP ERP Central Component (ECC) to SAP APO using the CIF model between supply site NA and IHDC. This transportation lane uses data shown in the second row of Table 2.
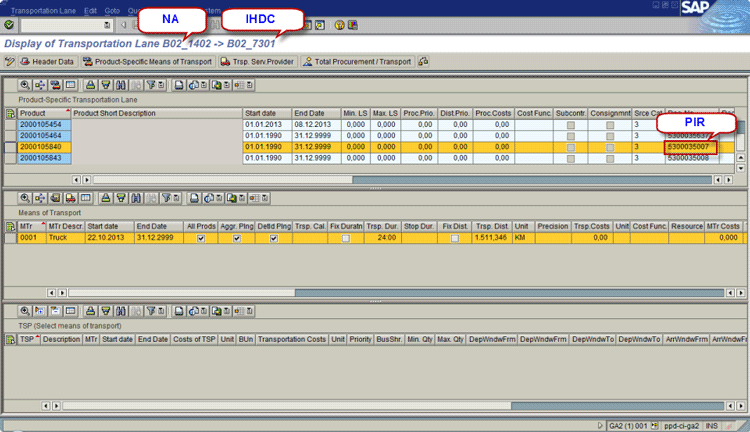
Figure 5
Transportation lane details
To create a transportation lane between IHDC and RWH using an SPK, execute transaction code n/sapapo/tl1. This action returns you to the screen shown in Figure 4. Enter 000 in the Model Name field, B02_7301 in the Start Location field, and B02_7313 in the Dest Location field. After you click the Display button, you can view the transportation lane details in the screen shown in Figure 6.
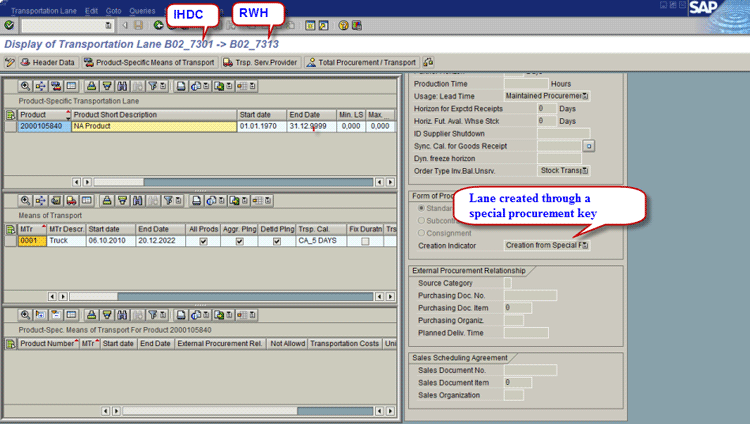
Figure 6
A manual transportation lane in SAP APO
The Supply Chain Network During Business Cutover
Figure 7 shows a planning scenario from October 2013. In this scenario, note that the demand signal to the supply site before 3PL go-live was sent to supply sites directly from the IHDC. The demand signal in the planning horizon beyond the go-live date was sent from the IHDC to supply sites NA via the 3PL to give forward visibility to supply sites that post go-live shipments which need to be sent to the 3PL.

Figure 7
Supply networks during cutover
Figure 8 shows a supply chain network created using the following transportation lane setup during business cutover period:
The key points are:
- The same PIR was extended to two distribution center codes: 3PL (new) and IHDC (old), creating two transportation lanes in APO after integration via CIF.
- Manually created transportation from 3PL to IHDC to send the demand signal to supply site NA so that stock or receipts at 3PL as well as IHDC are netted.
- Manually created blocked transportation lane from IHDC to 3PL to account for in-transit inventory associated with stock transfer order created in ECC to send the stock from IHDC to 3PL. The stock transfer order on integration with APO created DistReceipt truck load builder (TLB) Confirmed (Distribution Demand Orders) at 3PL and DistDemand TLB Confirmed (Distribution Demand Orders) at IHDC. The transportation was blocked to eliminate the cyclic relationship between IHDC and 3PL during low-level code generation.
- The demand plan was dropped to IHDC until go-live. After go-live it was dropped to the 3PL.
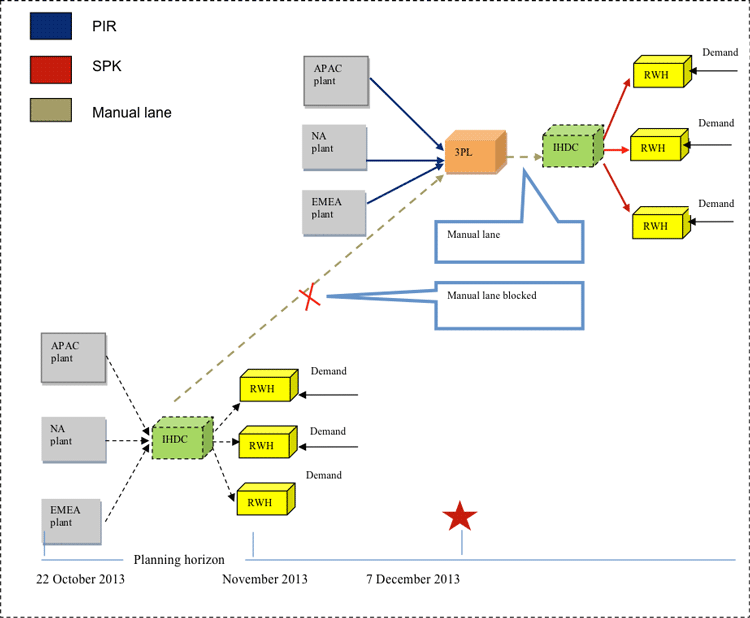
Figure 8
Supply chain network during cutover period
Table 3 lists data used for a transportation setup during cutover.
From location
|
To location
|
Valid start date
|
Valid end date |
Master data
|
Description
|
APAC
|
IHDC |
01/01/1990 |
31/12/9999
|
PIR1 |
PIR |
APAC
|
3PL
|
12/08/2013
|
31/12/9999 |
PIR1
|
PIR |
NA
|
IHDC |
01/01/1990 |
31/12/9999 |
5300035007
|
PIR |
NA
|
3PL
|
12/08/2013 |
31/12/9999 |
5300035007
|
PIR
|
EMEA
|
IHDC
|
01/01/1990 |
31/12/9999 |
PIR3
|
PIR
|
EMEA
|
3PL |
12/08/2013 |
31/12/9999 |
PIR3
|
PIR
|
IHDC |
RWH_01 |
01/01/1990 |
31/12/9999 |
SPK11 |
SPK |
IHDC |
RWH_02 |
01/01/1990 |
31/12/9999 |
SPK21 |
SPK |
IHDC |
RWH_03 |
01/01/1990 |
31/12/9999 |
SPK31 |
SPK |
3PL
|
IHDC |
01/01/1990 |
31/12/9999 |
Manual |
Open
transportation lane in APO |
IHDC |
3PL |
01/01/1990 |
31/12/9999 |
Manual |
Blocked status transportation lane in APO |
Table 3
An example of transportation setup during cutover
Note
The data listed in the third and fourth rows of Table 3 for From location, To location, and Master data were used in the solution.
Master Data
Three key master data records were created: a PIR, manual transportation lanes, and quota arrangement.
PIR
Figure 9
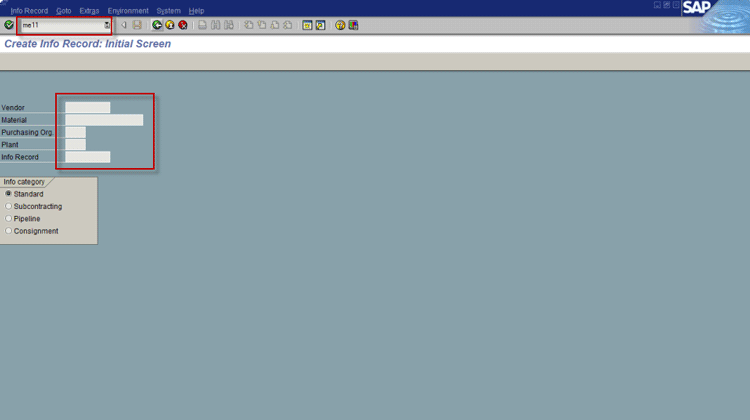
Figure 9
Create a PIR in the ECC system
Figure 10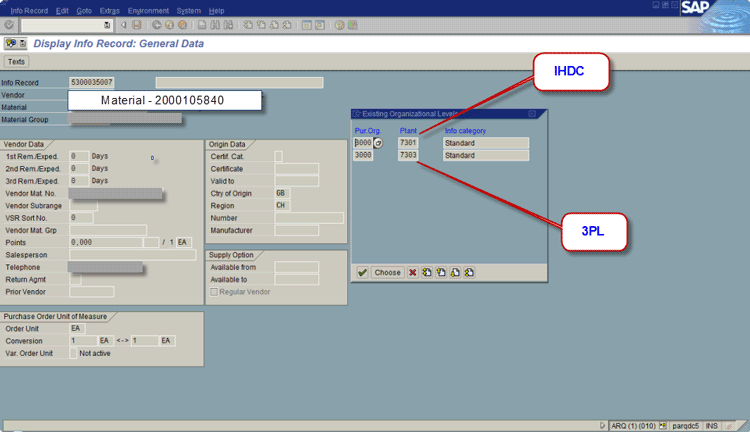
Figure 10
PIR extended to two receiving locations: IHDC and 3PL
Figure 10 shows that one PIR has been extended to two plant codes (IHDC and 3PL) that are for one vendor supplying two destination locations. This setup is required for enabling the supply sites to send stock to both IHDC and 3PL during the cutover phase.
To send the demand signal upstream to supply site NA from IHDC via 3PL, you need to create a transportation lane manually in the SAP APO system. To do this process, execute
transaction code /n/sapapo/tl1.
Figure 11 shows the fields required and steps to follow for creation of a manual transportation lane for a product. Populate the Model Name, Start Location (3PL), and Dest Location (IHDC) fields as shown in Figure 11.
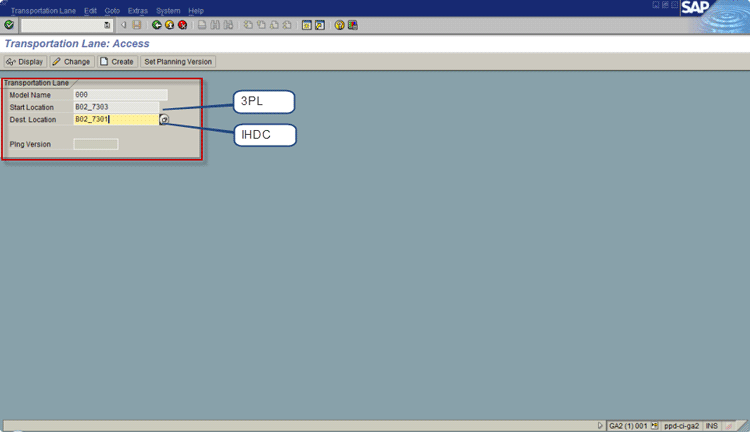
Figure 11
Create a transportation lane
Click the Create button to open the screen shown in Figure 12.
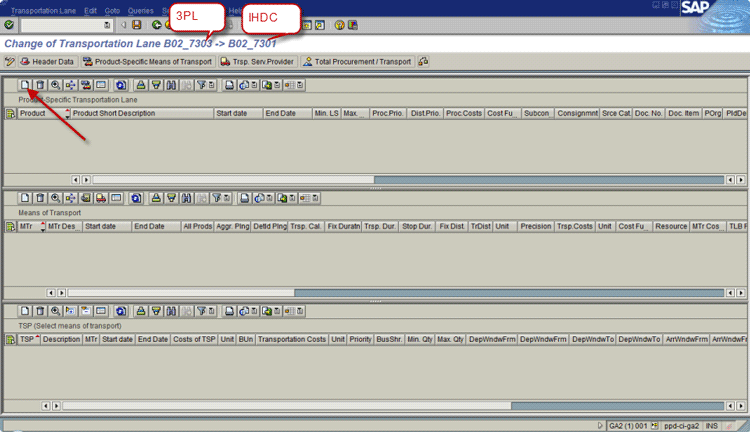
Figure 12
Create a manual product-specific transportation lane
In this screen, click the create icon (the arrow points to this icon in Figure 12). This action opens a new screen on the right as shown in Figure 13.
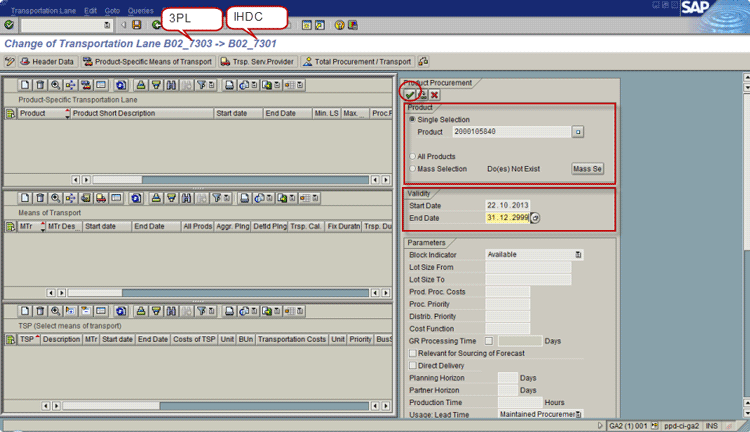
Figure 13
Enter product-specific details for the transportation lane
In Figure 13, enter the product code for which the transportation lane is being created in the Product field. In the Validity section, enter values in the Start Date and End Date fields. After entering this data, click the enter icon (the green check mark). This action opens the screen shown in Figure 14.
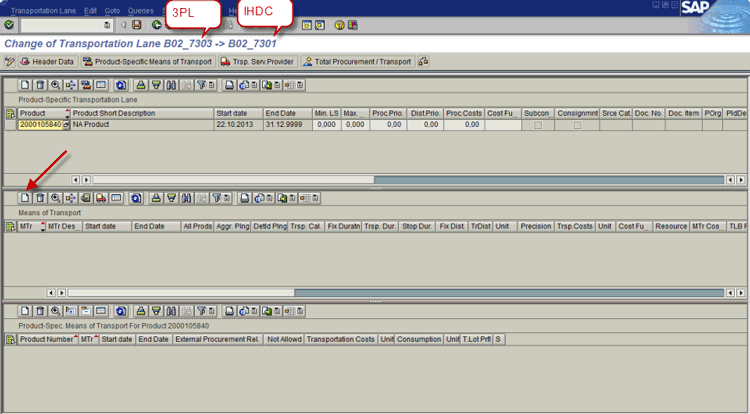
Figure 14
Maintain a product-specific transportation entry
Click the create icon to create the means of transport.After you click the create icon, a new subscreen opens to the right as shown in Figure 15. In the subscreen, specify a code for the means of transport in the Means of Trans. field and populate the Start Date and End Date fields. In the Control Indicator section, leave the default parameters selected as shown in Figure 15.
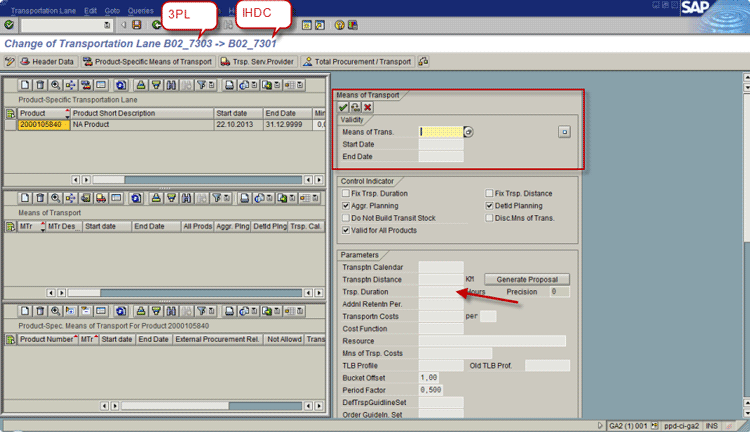
Figure 15
Enter details to create the means of transport
In the Parameters section, enter a value for a transportation duration in the Trsp. Duration field. Click the enter icon. This action displays the details of the means of transport created as shown in Figure 16.
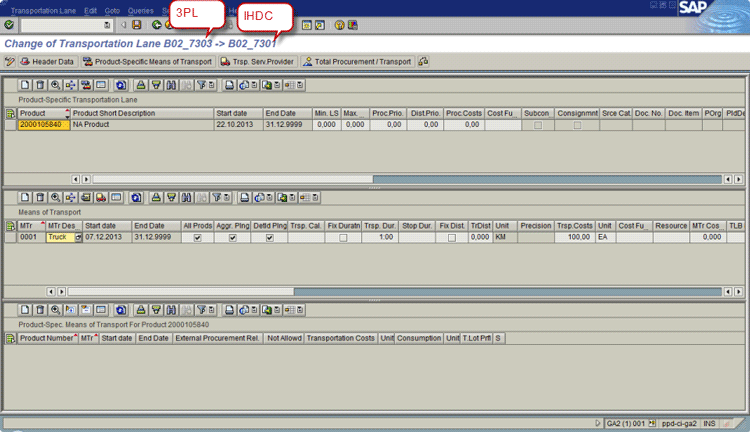
Figure 16
Create a means of transport in the transportation lane
The transportation lane also is created in SAP APO system after sending a PIR from the ECC system. Figure 17 shows the transportation lane between NA and 3PL created after integrating the PIR in ECC. The means of transport (MOT) was set as effective on 22.10.2013 (the date before the cutover date of December 1 of the last shipment from NA to IHDC) so that the supply site can deploy into 3PL if all the demand from IHDC within the horizon before the go-live date of December 7 has been deployed by the supply site. In Figure 17, note also that the PIR number is the same for the lane NA to IHDC.

Figure 17
Create the transportation lane with integration of a PIR
Figure 18 shows the transportation lane manual created in APO with a blocked status. This lane was created to receive manually created stock transfer orders in ECC to ship stock from IHDC to 3PL. Although the lane was locked, it still allowed STO to come from ECC without any error.
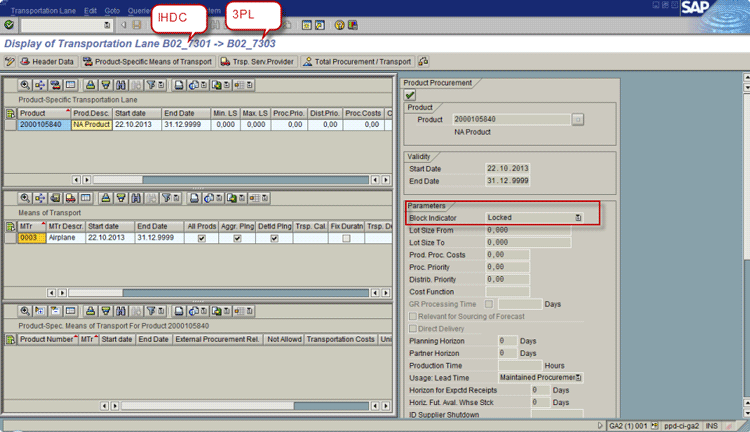
Figure 18
A manually created transportation lane between IHDC and 3PL
Inbound Quota Arrangement
The inbound quota arrangement was used to define the validity period for the source of supply. The quota arrangement shown in Figure 19 was created using the setup shown in Table 4.
Product code
|
From location
|
To location
|
From date
|
To cutover date (MM/DD/YYYY)
|
Master data
|
P001
|
APAC
|
IHDC |
01/01/2010
|
12/06/2013 |
PIR1 |
2000105840
|
NA
|
IHDC
|
01/01/2010 |
12/06/2013
|
PIR2 |
P003
|
EMEA |
IHDC |
01/01/2010 |
12/06/2013
|
PIR3 |
P001
|
3PL
|
IHDC |
12/07/2013 |
31/12/9999
|
Manual transportation lane in APO
|
2000105840
|
3PL
|
IHDC |
12/07/2013 |
31/12/9999
|
Manual transportation lane in APO
|
P003
|
3PL |
IHDC |
12/07/2013 |
31/12/9999
|
Manual transportation lane in APO
|
Table 4
An example of quota arrangement setup
The quota was set for IHDC to source from NA until 06.12.2013 using external procurement relationship/PIR. The quota was set with a validity date effective 07.12.2013 to 31.12.9999 for IHDC to source from 3PL so that the demand signal goes to NA via 3PL. The purpose was that supply sites would know that stock should be sent to the new ship to address of 3PL after December 7. The cutover date in the second row and the From date in the fifth row in Table 4 can be seen in Figure 19 and were used in the solution design.
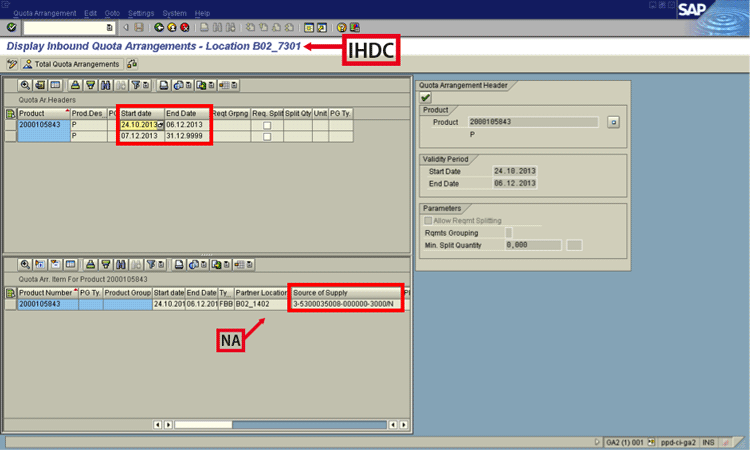
Figure 19
Quota arrangement setup
To create a quota arrangement, execute transaction code /sapapo/scc_tq1. In the Quota Arrangement section of the screen that appears (Figure 20), specify the Model as 000 and the Location as B02_7301 (the IHDC). In the Version section, select the Version Independent button, and in the Quota Arrangement Direction section, select Inbound Quota Arrangements.
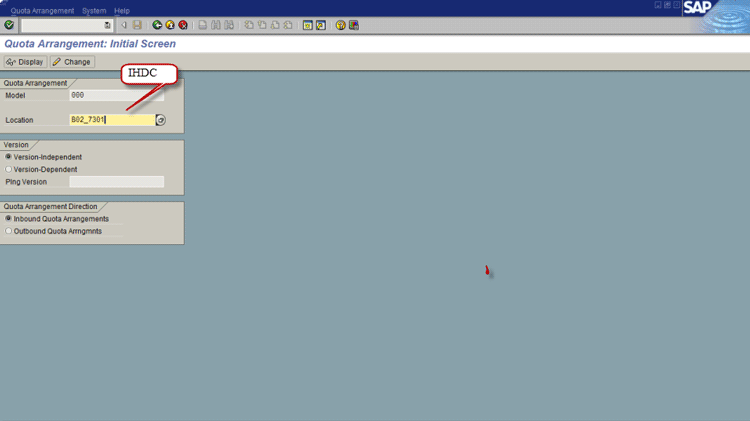
Figure 20
Choose the quota arrangement type and location
After entering these values, click the Change button to create the quota arrangement. This action opens a new screen (Figure 21).
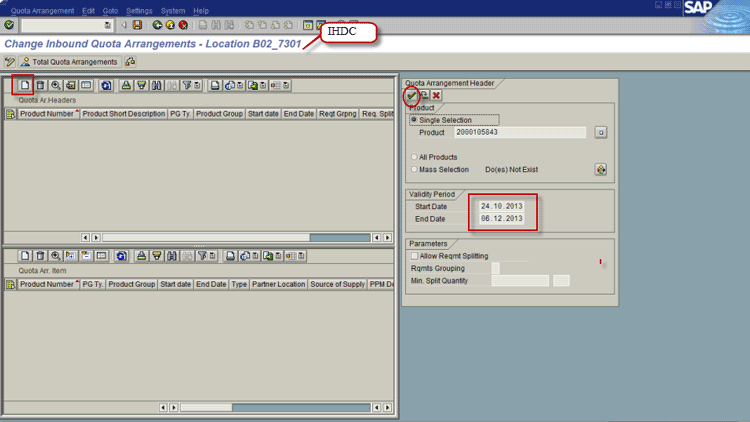
Figure 21
A quota arrangement header with a validity period before the 3PL go-live
In Figure 21, click the create icon to create a quota arrangement header record. After you click this icon, a subscreen opens to the right. In this subscreen, enter the product code in the Product field, and in the Validity Period section, enter values for the Start Date and End Date of the quota. Click the enter icon to create the first quota header record for the period 24.10.2013 to 06.12.2013.
To create another header record for the source supply after the 3PL planned go-live date, click the create icon again. This action opens the subscreen on the right (Figure 22). Enter the values as shown in Figure 22 and then click the enter icon.
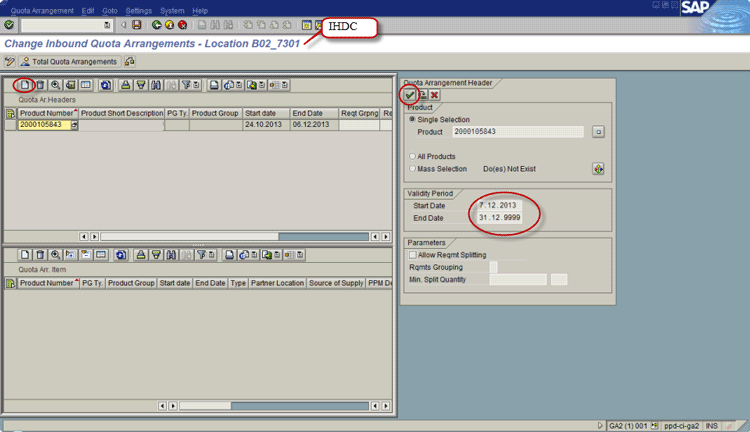
Figure 22
A quota arrangement header with a validity period after the 3PL go-live
Figure 23Figures 2223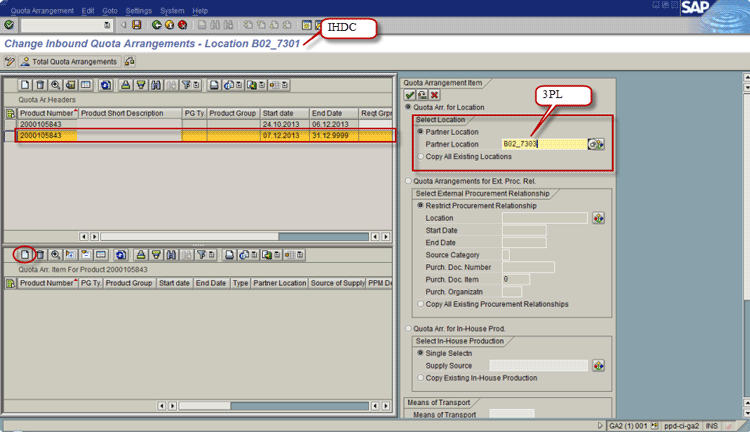
Figure 23
Assign 3PL as the source of supply for post 3PL go-live period
Similar to the steps discussed in Figure 23, select the first quota arrangement header record and then click the create icon in the lower half of the screen. This action opens the subscreen to the right. In the subscreen, select the radio button Quota Arrangements for Ext. Proc. Rel. and then click the shuffler icon . This action opens a subscreen called Selection of a Source of Supply. In this screen, select the external procurement relationship of B02_1402 (the NA supplier) as the source of supply created using the PIR and then click the enter icon (Figure 24).
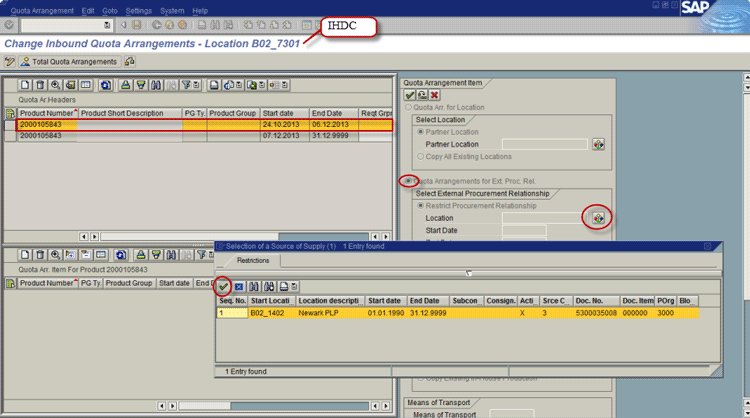
Figure 24
Select B02_1402 (the NA supplier) as the source of supply for before the go-live period
In the next screen (Figure 25), click the enter icon again. This action opens the screen shown in Figure 26.
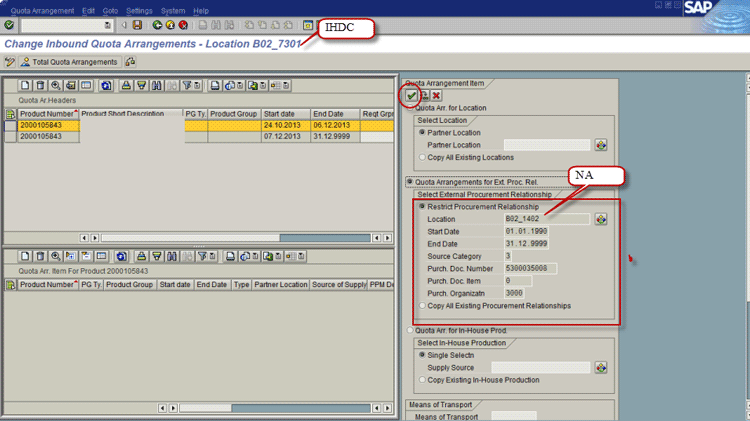
Figure 25
Select B02_1402 (the NA supplier) as the source of supply for before the go-live period
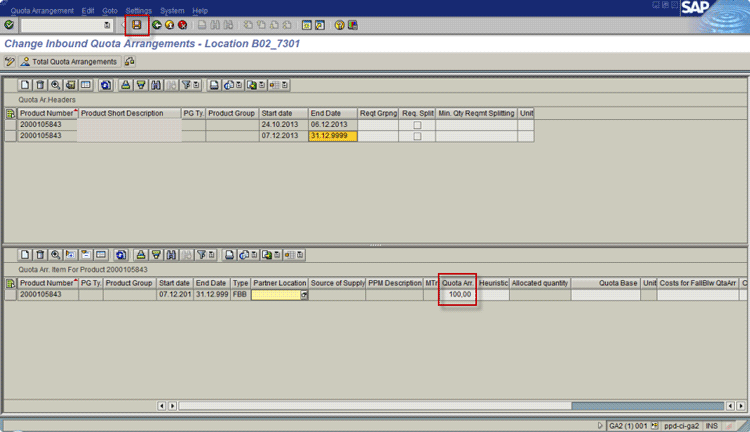
Figure 26
Enter a quota arrangement quantity
In Figure 26, in the field under the Quota Arr. column, enter a quota arrangement quantity of 100 so that 100 percent of the requirements at the IHDC are sourced from the NA supplier. Click the save icon.
SNP Heuristics Results
After master data setup is complete, execute SNP heuristics to generate the supply plan in the network. To execute SNP heuristics, use transaction code /n/sapapo/sdp94. In the screen that appears (Figure 27), click the shuffler icon to load the product and location in the planning book.

Figure 27
How to load product and location in SNP planning book
The NA supply site received a demand signal from the IHDC before Dec 7, 2013. Figure 28 shows the planning results after an SNP heuristics run.

Figure 28
Planning results after an SNP heuristics run
Figure 29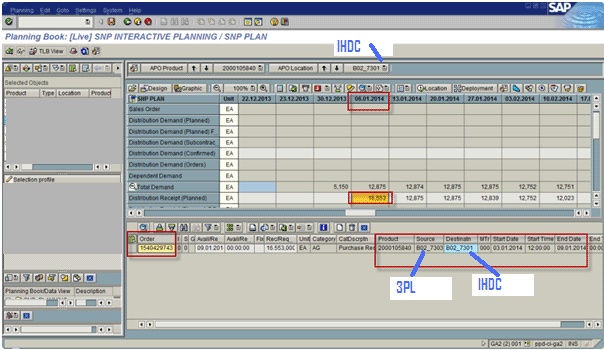
Figure 29
SNP heuristics results
Figure 30 shows that demand on 30.12.2013 is passed from the IHDC via the 3PL to the NA supplier.
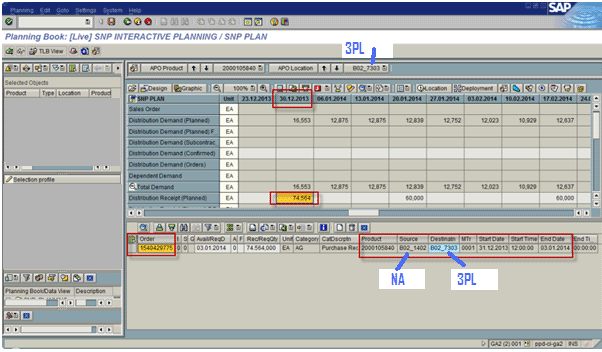
Figure 30
SNP heuristics results
Deployment Heuristics Results
After a supply plan is generated by running heuristics, deployment is executed to confirm the supply against demand. Deployment can be executed interactively using transaction code /sapapo/sdp94 or run in background mode using report /SAPAPO/RMSDPDEP. Figure 31 shows that on an interactive and background deployment run, the system deployed stock to the IHDC for demand before 06.12.2013 and generated receipts confirmed elements with a destination as the IHDC.
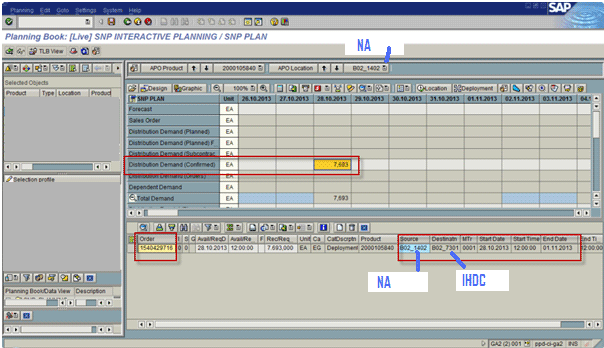
Figure 31
Stock deployed before the 3PL planned go-live date from the NA supplier to the IHDC
Figure 32 shows that the deployment run deployed stock to the 3PL demand after 06.12.2013 instead of the IHDC and generated receipts confirmed elements with a destination as the 3PL.
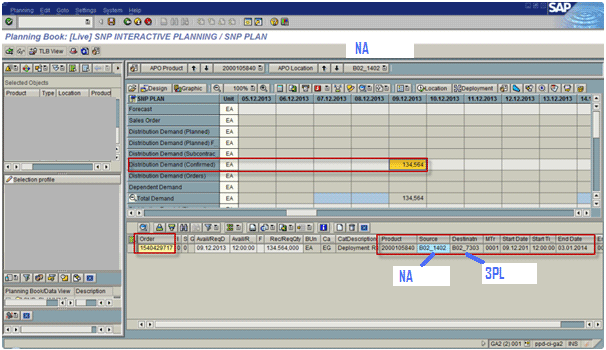
Figure 32
Stock deployed to the 3PL instead of the IHDC
Figure 33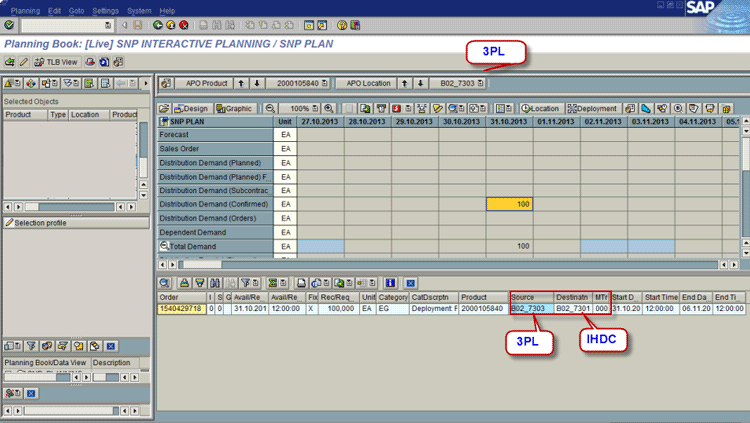
Figure 33
Manual deployment from the 3PL to the IHDC to avoid double demand
Truck Load Builder Purchase Order Creation
The truck load builder (TLB) transaction is used to create a stock tranport order or purchase order (PO) from the customer site to the supply site. The transaction code /SAPAPO/SNPTLB or report /SAPAPO/RMSDPTLB can be used to schedule a TLB run in the background.
Figure 34 shows the deployment confirmed receipts in the TLB transaction. Deployment confirmed receipts can be converted to a purchase order after selecting the deployment receipts and clicking the TLB button.
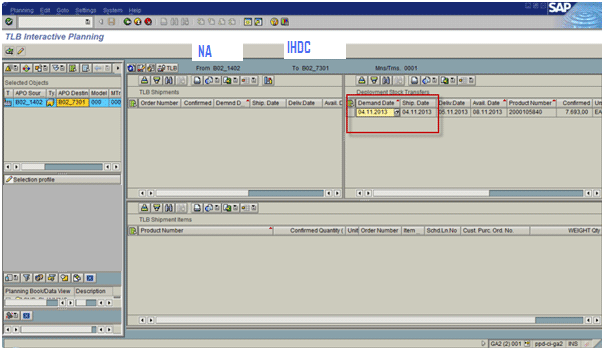
Figure 34
Deployment stock transfer to IHDC
Figure 35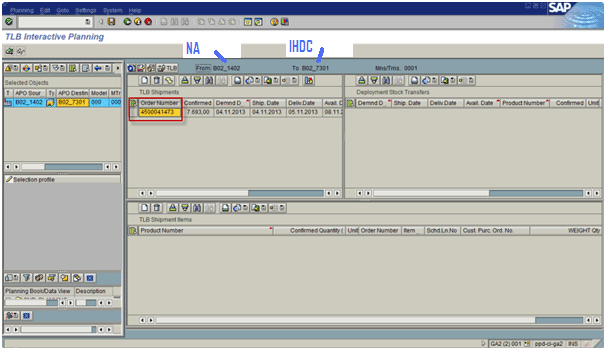
Figure 35
TLB shipment to IHDC
Figure 36 shows the confirmed receipts for transferring stock from the NA supplier to the 3PL after the planned 3PL go-live.
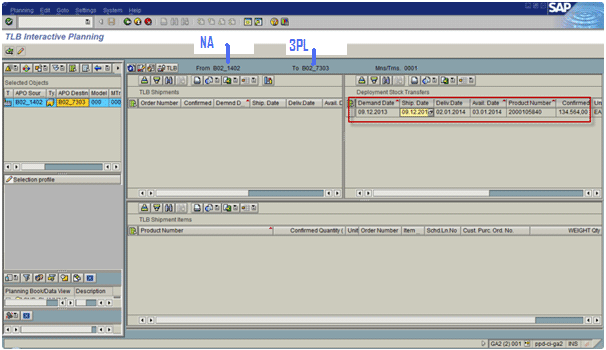
Figure 36
Deployment of stock transfers to the 3PL
Figure 37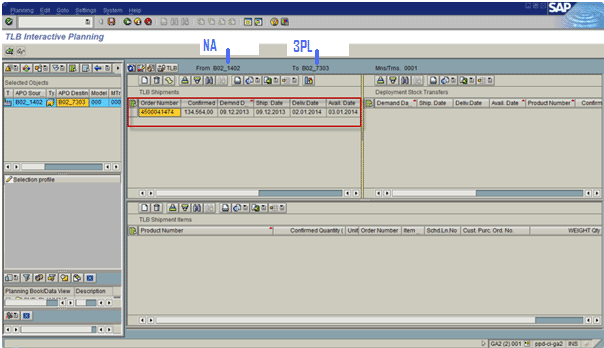
Figure 37
TLB shipments to 3PL
The Supply Chain Network after 3PL Business Go-Live
After go-live in December, location code IHDC was removed from the supply network in APO and replaced with 3PL. The lanes pointing from supply sites into 3PL created during cutover using a PIR were continued and lanes connecting 3PL to the regional warehouse (RWH 01, RWH 02, RWH 03 were created assigning new SPKs in ECC material master and re-integration of these materials to APO using the core interface.
Table 5 lists the data used for a transportation lane setup to model a new supply chain. The PIR in the second row of Table 5 was used to establish the network between supply site NA/B02_1402 and B02_7303 after go-live. This PIR can also be seen in Figure 10.
From location
|
To location
|
Valid start date
|
Valid end date |
Master data
|
Description
|
APAC
|
3PL |
01/01/2010 |
31/12/9999
|
PIR1 |
PIR |
NA
|
3PL
|
01/01/2010
|
31/12/9999 |
5300035007
|
PIR |
EMEA
|
3PL |
01/01/2010 |
31/12/9999 |
PIR3
|
PIR |
3PL
|
RWH_01
|
NA |
NA |
SPK13
|
SPK
|
3PL
|
RWH_02
|
NA |
NA
|
SPK23
|
SPK
|
3PL
|
RWH_03 |
NA |
NA
|
SPK33
|
SPK
|
Table 5
An example of transportation setup after go-live
Figure 38 shows the supply chain networks that were established and used beyond 3PL go-live throughout the planning horizon. The network between supply sites and 3PL was created using a PIR. The network between the regional warehouse and 3PL was created using an SPK.
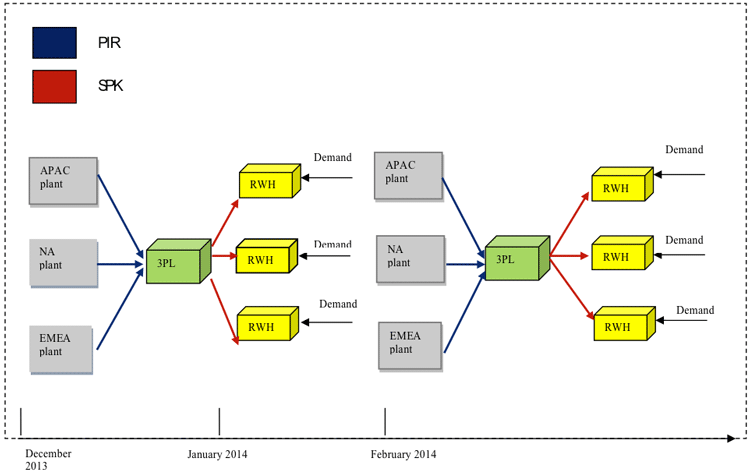
Figure 38
Supply chain network after 3PL go-live
Supply Chain Scope Outsourced Successfully
Leveraging SAP APO standard functionalities such as transportation lanes, quota arrangement heuristics, deployment, and TLB, the company successfully outsourced IHDC operations to 3PL with the following highlights:
• Supply chains for 38 brands with 150 SKUs managed by approximately 50 users across the 10 supply sites located in different parts of the globe were integrated into 3PL without any customer impact and no stockouts at IHDC or 3PL.
• More than 250 stock transfers for 1.5 million units of inventory were transferred over a two-month period using APO to net out the stock levels between the two plants to send the right demand signal back to the supply site.
• No inventory build was required for this transition due to the seamless transition from the old DC to the new DC in APO.
Note
I would like to thank Sawdah Amode, a supply chain integrator, and Glyn Harrison, an SAP SCM consultant at a leading pharmaceutical company, for their help and contributions to the project that I wrote about in this article.
Manish Thukral
Manish Thukral is is a certified SAP SCM consultant with more than 10 years of hands-on experience in the SAP Supply Chain Management (SCM), SAP Advanced Planning and Optimization (SAP APO), and SAP Integrated Business Planning suite of products, such as SAP APO Demand Planning (DP), SAP APO Supply Network Planning (SNP), Core Interface (CIF), Global Available to Promise (GATP), SAP Integrated Business Planning for demand, SAP Integrated Business Planning for supply, SAP Integrated Business Planning for sales and operations planning, and SAP Integrated Business Planning Supply Chain Control Tower. He has experience with multiple full life-cycle implementations and multiple projects.
Manish also is an APICS certified consultant with experience in functional areas of production planning, warehouse management, inventory management, demand planning, supply planning, sales and operations planning, and available-to-promise spanning across apparel, consumer packaged goods (CPG), fast-moving consumer goods (FMCG), and pharmaceutical industry sectors.
You may contact the author at thukralmanish@yahoo.com.
If you have comments about this article or publication, or would like to submit an article idea, please contact the editor.