Learn about major enhancements introduced in SAP Transportation Management (SAP TM) 9.1 that will help in managing transportation process across industries. Find enhanced transportation planning functionality that enables you to efficiently manage truck loads. Find out how functionalities such as the collaboration portal and strategic freight procurement enable close collaboration with your partners. Discover how better integration with SAP core modules facilitates the execution of end-to-end transportation processes.
Key Concept
SAP Transportation Management (SAP TM) 9.1 includes features related to industries such as rail, ocean, and parcel transportation. It also includes enhanced integration with peripheral modules, such as SAP Extended Warehouse Management (SAP EWM), ERP, SAP Global Trade Services (SAP GTS), and Customer Relationship Management (CRM).
Before 2012, SAP Transportation Management (SAP TM) supported only core transportation processes for shippers. In 2013, SAP released SAP TM 9.0, which offered a set of features for the freight forwarding industry, such as ocean and air freight management, freight settlement with carriers, and related enhancements to SAP Event Management.
SAP TM 9.1 includes additional enhancements specifically focused on the rail and parcel industries, along with a set of features applicable to the shipper and freight-forwarding industries. This release also brings SAP Extended Warehouse Management (SAP EWM) and SAP Event Management much closer via tighter integration with SAP TM.
New features in SAP TM 9.1 are categorized into these areas:
- Cross-industry functionalities
- Industry-specific solutions
- Enhanced integration
We now discuss some of the key new functionalities introduced in SAP TM 9.1, focusing on key functionalities in each category.
Cross-Industry Functionalities
Cross-industry functionalities include strategic freight management, a collaboration portal, load planning (vehicle scheduling and routing), and capacity management.
Strategic Freight Management
Strategic freight management includes procuring and selling freight. The functionality of freight procurement only involves managing freight contracts with a carrier for ocean, air, or road transportation for a specific trade lane and commodity combination.
This process starts with request for quotation (RFQ) generation either based on existing freight agreements or templates. The approval workflow for the freight agreement RFQ also triggers various statuses in RFQ, such as in process, request approval, awaiting approval, and approved.
The RFQ is then published to multiple carriers for review. The carriers respond with capacity and rate information that can be tracked in the Comparison Cockpit. A versioning capability allows multiple negotiation rounds with a carrier. The Comparison Cockpit also enables you to compare rates for individual or multiple RFQ items. A response comparison builds rank by charge type (representing type of costs in RFQ [e.g., pickup, base, or loading charges]).
SAP TM 9.1 introduces an optimizer that assigns transportation volume (as specified in an RFQ item) to carriers while minimizing total transportation costs. Business share strategies (e.g., minimum or maximum allocations per carrier) can influence the output of the optimizer. Optimization or simulation of estimated transportation costs per carrier can be run for an individual item or the entire RFQ.
After a carrier is chosen, a new freight agreement can be generated based on RFQ information for a specific carrier. Figure 1 outlines various stages of a freight procurement process.
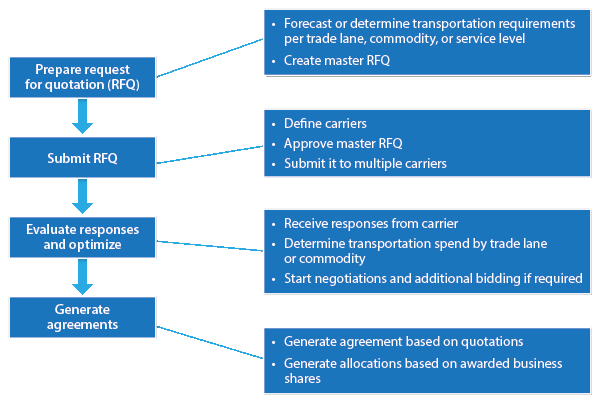
Figure 1
Stages of the freight procurement process
Although strategic freight management is more applicable to freight-forwarding companies (OEMs with large transportation requirements), companies can use what-if scenarios to compare transportation spends based on RFQ responses. Automatic creation of a freight agreement based on an RFQ response is a feature that reduces administrative overhead. Note that you need to consider change management as well as the interfacing effort if you wish to publish or receive RFQ-related information to carriers.
The Collaboration Portal
Business partners use a collaboration portal to participate in the tendering process. SAP TM 9.1 introduces a browser-based collaboration portal solution that allows participation by the shipper as well as carriers to carry out the tendering process. It features two types of business documents:
- Freight request for quotations (shipper assigned it to specific carrier)
- Freight quotations (the carrier’s response to an RFQ)
Carriers can accept or reject an RFQ or even initiate changes in the original quote. Relevant RFQ details (such as trade lane, commodity, or date times) can be fetched onto the portal. The carrier submits a response to the RFQ, which becomes a freight quotation in the portal. Further statuses (such as awarded, pending, and rejected) can be monitored via the quotation work list.
The collaboration portal opens selective transportation data from the organization to business partners. You need to take into account your company’s security and authorization policies while allowing a partner’s user IDs into the collaboration portal. You might consider embedding your portal’s URL into your existing supplier’s or carrier’s portal as a separate link. It is important to consider change management and training during the initial onboarding. SAP offers limited customizations in this area, so you can expect minimal development and screen modifications as far as a collaboration portal is concerned.
Consider a scenario in which a large manufacturing company is looking at a collaboration portal for facilitating its transportation management business processes mainly in four areas:
- Self-billing, invoice submission, and dispute management for carriers: The company is using standard SAP TM functionality for freight settlement that in turn creates a purchase order and service entry sheet in the ERP Central Component (ECC) system for carrier payment. For many carriers the company follows a policy of self-billing (i.e., the carrier bills are automatically created when the materials are delivered to the customer and the carrier does not need to submit a separate invoice). Any disputes that arise during the billing process can be handled using the collaboration portal. Carriers can log in to the portal and log any issue related to invoices, and the company can respond.
- Event notification and reporting of events by carriers: Freight-order related events are reported through the collaboration portal. Carrier events such as freight order confirmed and proof of delivery (POD) can be tracked through the portal.
- Strategic freight procurement: The company had a number of requirements and a few of them were partially enabled through the collaboration portal. If a company does not have a carrier contract, it follows an RFQ process in which selected carriers are expected to provide a quotation. A carrier can view the RFQ published by the company and submit the freight quotation through the portal. The acceptance and rejection of a freight RFQ is enabled by the collaboration portal.
- Track and trace of consignments: Carriers update the status of a consignment, especially the delivery status, through the collaboration portal. If there are categories of materials for which the company has higher track and trace requirements, POD can be uploaded in the collaboration portal by carriers.
Lessons learned from the collaboration portal: SAP TM at this point supports collaboration portal functionality only for freight orders and not for freight bookings. This means that for certain modes of transport, such as maritime for which SAP recommends the use of freight booking as the object, you cannot use the collaboration portal.
Load Planning
SAP TM 9.1 introduced enhanced optimizer features that include not just total weight and volume, but also ensure that a freight order fits onto a truck in terms of dimensions, weight, and load distribution.
The load optimizer also gives 3D load planning results along with the exact location of a cargo item within a truckload. The load optimizer now checks dimensions (length, width, and height), weight, stackability, and axle load distribution along with specific business rules for stacking and loading. It also includes locations (loading or unloading sequence).
Integration with Visual Business 2.1 now gives a 3D view of the load plan with location of freight units. Visual Business is the user interface technology that visualizes data from the SAP system and external data sources in a single screen. It also helps to visualize the entire transportation network along with the planned route of the freight order
For this purpose, new layouts (road freight order hierarchy and load plan) have been introduced in the Transportation Cockpit.
To enable axle load distribution via the optimizer, additional fields have been introduced in the resource master data, such as Tare Weight (empty vehicle weight), Cargo Body Distance (from front to beginning of loading space), and First and Second axle group details, including distance between axles and maximum and minimum weight on the group. Capacity details, such as internal length, width, and height, are also now mandatory to maintain for load planning.
Planning profiles now also have load-planning settings that include business rules (e.g., height difference within a row or deviations). Load planning is now done at the Item or Pallet levels. These levels are essentially main cargo items assigned to freight units.
To configure settings for load planning, navigate to the Transportation Cockpit based on the selection profile and page layout settings. The Transportation Cockpit can be accessed by following menu path Planning > Worklist > Planning > WDY_APPLICATION – Transportation Cockpit. Double-click the icon beside WDY_APPLICATION – Transportation Cockpit to access the Load Planning screen in the Transportation Cockpit (Figure 2).
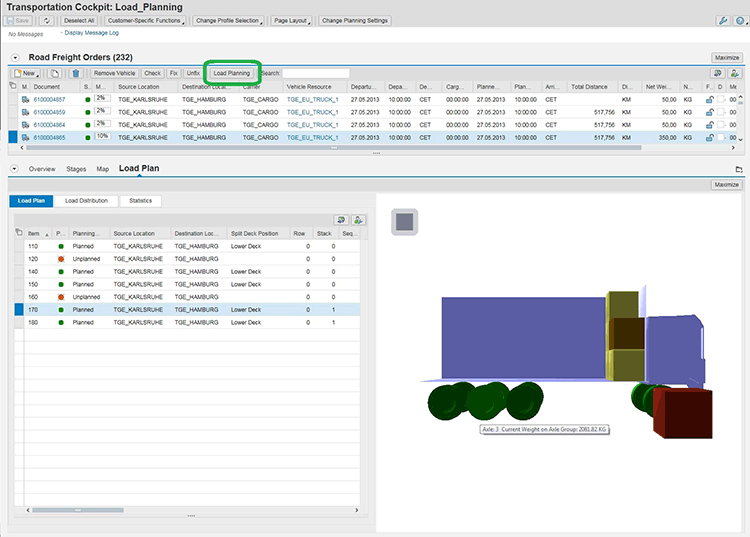
Figure 2
Load planning in the Transportation Cockpit
In Figure 2, select a freight order (e.g., 6100004865) and click the Load Planning button. You can see your selected order in the Load Plan tab of Figure 2.
The planner can now see how many items can be fitted in the truck. Therefore, the planner can load the remaining forwarding orders until the truck is full.
Planning profiles (including load plan) can be assigned to freight order type configuration. Therefore, load planning can be triggered from a freight order user interface (UI) as well. This load plan is integrated with SAP EWM for further execution.
Load-building functionality is closely integrated with transportation planning in SAP TM. It also relies extensively on business data related to loading such as space- and weight-related factors associated with transportation resources such as trailers and trucks. You should consider additional effort to set up what-if scenarios or data preparation as well as in training transportation planners.
Consider this example: A leading consumer goods company is implementing SAP TM 9.1 for meeting a number of load-building requirements. The requirements are around stackability, load balancing, pallet building, and packing materials. The company evaluated a number of standalone load-building solutions and then zeroed in on SAP TM 9.1 as the solution is integrated with overall transport planning and route optimization.
Note
In simple terms, stackability means planning loads in such a way that a light product is stacked on top of a heavy product to ensure maximum space utilization of the vehicle. In my example, the company had a set of stackability norms that differed by product group and the expectation from the solution was to take care of this while proposing loads and deliveries. The TM 9.1 functionality of 3D load plan visualization using SAP Visual Business was used to meet this requirement.
Load Balancing
In my example, the company’s load-balancing requirement was to distribute pallets across the vehicle to ensure safe axle weights and optimal use of space. The company also needed an understanding of the weight specification of each trailer type and of how much weight the vehicle can safely hold. SAP TM 9.1 Load Builder was used to maintain a variety of business rules for load balancing.
Beyond this, the company also had the following load-building requirements around the ability to:
- Manually build loads and override system-created loads
- Select from a list of supported equipment and assign it to load during planning
- Calculate pallet space and optimize the number of pallet spaces required
- Manage conflicting freight classes such as hazardous materials. This is managed through the dangerous goods classification and management functionality
- Convert orders in different units of measure (UOMs) to pallets and pallet spaces. In this case the customer orders come in different UOMs, such as ton, KG, or M3. However, pallets are the common units for all movements.
In my example, the company also had a few requirements around pallet building, which is a process step before the truck or trailer load planning, involving the need to build the pallet itself in SAP TM. The company could not address these requirements with current SAP TM 9.1 functionality. Therefore, it decided to continue with its existing manual process for this step.
This gap in the SAP TM solution is addressed in the most recent version (SAP TM 9.3). SAP TM 9.3 offers a pallet-building functionality before load building. A new product master data transaction is available called Define product package assignment. In SAP TM 9.3, you execute transaction code /SCMB/PB_PRD_PKG and follow menu path Master Data > General next to Define Product. Within this transaction, you can define a combination of product, business partner, and location for which a package or pallet can be built.
Now, we discuss industry-specific functionalities introduced by SAP TM 9.1.
Industry-Specific Functionalities
SAP TM 9.1 includes the following industry-specific solutions:
- Quotation and contract management, railcar management, rail order management, rail charge management, and invoicing for the rail industry
- Multi-pick and multi-drop ocean bookings and consolidation of transportation demands at the shipper and consignee for the ocean carrier industry
- Parcel management process, including transportation planning, manifest creation, parcel shipment and tracking, and invoicing for Parcel/Courier Industry
Railcar Industry
SAP TM 9.1 includes the following functionalities for the rail car industry:
- Forwarding order management
- Freight order management
- Railcar unit tracking
Forwarding Order Management
Since SAP TM 9.1, new shipping types (Intermodal Rail – 30 for Partial Car Load, Carload-31 for Full car load) have been introduced for rail scenarios (Figure 3). Shipping types are specific to the mode of transport, so they work in a way that is very similar to less container load (LCL) or full container load (FCL) for ocean carrier freight or unified loading device (ULD) or loose – (less than ULD) for air freight. To reach the shipping type, follow menu path SAP Transportation Management > Transportation Management > Forwarding Order Management > Define Shipping Types.
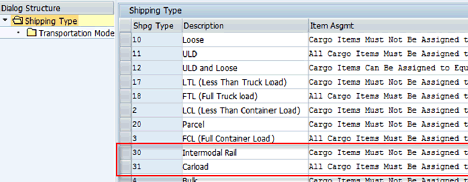
Figure 3
Addition of rail-specific shipping types
In rail orders, the equipment types used are railcar items, so categories such as containers, packages, and products are directly assigned to railcar items. A new item category, passive vehicle resource, has been introduced for railcars. The vehicle type is further assigned to the railcar, which provides physical properties such as payload weight or internal length and width to this item.
New personal object worklist (POWL) queries for rail forwarding orders have been introduced. They provide easy search and filter criteria based on the mode of transport as rail.
In SAP TM 9.1, a contract between shipper and rail carrier can be represented by a forwarding agreement. A forwarding agreement pertains to routes covered by the rail carrier’s schedule. A forwarding order item can be linked to a forwarding agreement. The forwarding order item adds ordered route or billing rates information to the forwarding order. A forwarding order item is also used further for charge calculation in rail forwarding orders based on those billing rates.
SAP TM 9.1 now offers three different ways of billing:
- A scenario in which all transportation charges are billed by an ordered carrier to the customer. The ordered carrier is the one who has the order from customer to move goods from location A to location B via rail.
- An interline rule 11 scenario in which all transportation stages are charged separately by executing carriers to customer (Rule 11 of American Rail Road Accounting mentions that rail services involving multiple executing carriers should be invoiced separately to maintain confidentiality of prices or contracts.) The executing carrier is the one who is physically involved in moving goods from location A to location B.
- A hybrid scenario in which a few stages are billed by an ordered carrier and other stages billed by an executing carrier.
Freight Order Management
A freight unit building rule in a rail forwarding order automatically creates railcar units. A railcar unit is a special type of equipment used in rail scenarios. It represents a single or a group of physical railcars. Railcar items are assigned to rail car units. A new resource/equipment tab has been introduced to capture capacity details, such as railcar resource assignment, gross, net, and tare weight. Commodity code details can also be maintained under railcar units. You can maintain a position in a train for specific railcar items.
Planners can now assign railcar units to a rail freight order either by using the Transportation Cockpit or by dragging and dropping a railcar unit onto a railcar resource. The Transportation Cockpit has new screen areas for Rail Car Unit Hierarchy, Rail Freight Order, Rail Freight Order Hierarchy, and resources such as railcars. SAP TM 9.1 includes search and filter functionality that facilitates a planner’s search for specific resources or freight orders. A new Utilization tab has also been introduced in the Freight Order Details screen. The Utilization tab enables users to monitor the extent that freight units have been loaded onto it.
Once planned, a rail freight order receives stage information from the railcar unit. This data is only source or destination information. Users can now assign routing to a rail freight order via search functionality available in the Freight Order UI. This UI fetches rail routes based on the freight agreement assigned to a specific carrier. After a route is selected, it also extracts freight agreement data such as additional stages, executing a carrier, invoicing a carrier, stage types, and charges. As you can see, this data is used further in charge calculation based on specific scenarios outlined above.
In a rail freight order, the executing carrier and invoicing carrier can be different. Therefore, it’s possible to maintain an executing and an invoicing carrier for each stage separately. During charge calculation, the invoicing carrier is used to determine freight agreements. The invoicing carrier generally has a freight agreement with a shipper or third-party logistics provider indicating rates for a particular trade lane. It is possible for physical trucking movements to be managed by a different set of carriers identified as executing carriers.
Railcar Unit Tracking
With SAP Event Management 9.0, Support Package 4, a new visibility process called resource tracking has been introduced to track vehicle resources or transportation units in SAP TM 9.1.
Note
SAP Event Management is closely integrated with SAP TM by means of a transportation visibility process and is a separate module in itself.
With resource tracking, resources such as containers or railcars assigned to various SAP TM documents can be tracked. A new resource event handler type (RES30_RESOURCE) monitors all the resources within SAP TM. This event handler type is created as soon as resource master data is created via the change notification agent. The change notification agent represents a trigger once corresponding SAP TM documents are changed. Further changes (updating or deletion) of resource master data are also reflected in SAP Event Management.
As soon as a resource is planned or assigned to an SAP TM document, corresponding expected events (e.g., arrival or departure of a freight order) are also populated on resource event handler types.
With SAP TM 9.1, a new application object type has also been introduced for transportation units. A transportation unit is a combination of multiple transportation resources assigned to one SAP TM document. For example, multiple railcar resources can be assigned to a railcar unit, which is assigned to one freight order. On the SAP EM side, they are still assigned to resource event handler.
Key functionalities are now available for tracking of a resource:
- Check availability of the resource
- Report events directly at the resource (e.g., container level events)
- Generate alerts at the resource when an unexpected event is reported (e.g., damage of the resource)
Because there are many events reported on the resource event handler as part of SAP Event Management, a new event date filter has also been introduced in the SAP Event Management web UI: the Tracking Scenario shown in Figure 4. To launch the SAP Event Management Web UI, follow menu path SAP Menu > SAP Event Management > Web Interface > Search (transaction code /N/SAPTRX/EM_START).

Figure 4
Railcar resource tracking via the SAP Event Management web UI
Although these features cover most of the requirements that the rail industry has been seeking, be ready to spend additional development and customization effort for rail car unit tracking. Based on our experience, such visibility processes can be used only as guidance or a starting point.
Freight order management is very useful feature and blends into transportation planning. It is convenient to allocate rail-car resources to freight orders and can be adopted with minimal customization.
Tracking of railcar resources adds to the amount of transportation-related data already tracked. You might size the SAP Event Management component, as data grows exponentially as more railcar units are tracked.
Ocean Carrier Industry-Specific Functionalities
Although the export and import process was introduced in SAP TM 9.0, functionality related to buyer’s consolidation is introduced as part of SAP TM 9.1. Buyer’s consolidation (Figure 5) is defined as sourcing goods from different suppliers and consolidating on the export side of operations. The consignee is expected to receive consolidated goods as a single unit on the import side.
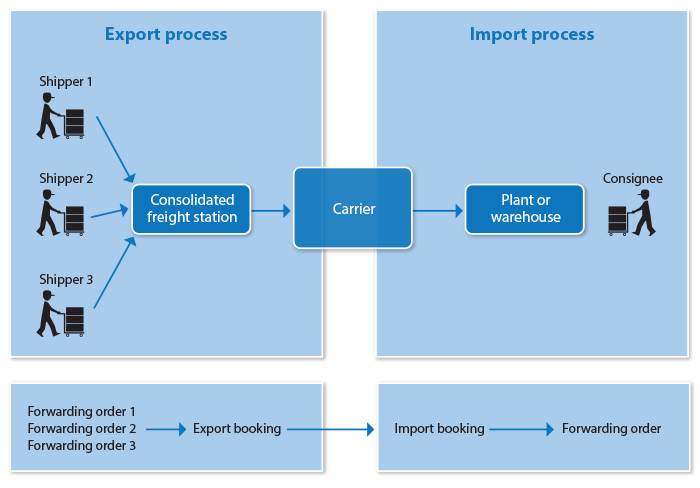
Figure 5
Buyer’s consolidation and de-consolidation of goods
For example, an export creates three forwarding orders and consolidates them into a single freight booking. A Shipped on Board or Uplift Confirmed status triggers the creation of an import forwarding order or freight booking. The import forwarding order contains an item and sub-items for each package. For sub-items, individual shippers are copied as business partners. Pickup stages are copied into the Stages tab per sub-item. Ordered or actual routes are copied from the export forwarding order per sub-item. The import forwarding order is created in draft status, which is set to In Process by the user. The import forwarding order can show multiple pick-up stages derived from multiple export forwarding orders. A logistics service provider (LSP) can charge LCL rates for pick-up and FCL rates for main leg or delivery.
An export business unit creates one forwarding settlement document to an import business unit, including one invoice for pickup (from three forwarding orders) and a main leg. The import business unit creates one forwarding settlement document, including pickup, main leg, or delivery to consignee.
In Free on Board Ship (FOB), Free Carriage and Freight (FCA), and Free Alongside Ship (FAS) scenarios, the export business units create three invoices for pickup or main leg to shippers. The import business unit creates one invoice that includes the main leg or delivery to consignee.
Shipper’s consolidation (Figure 6) is defined as sourcing consolidated goods from a single shipper and de-consolidating it at import operations. It’s then distributed across multiple consignees.
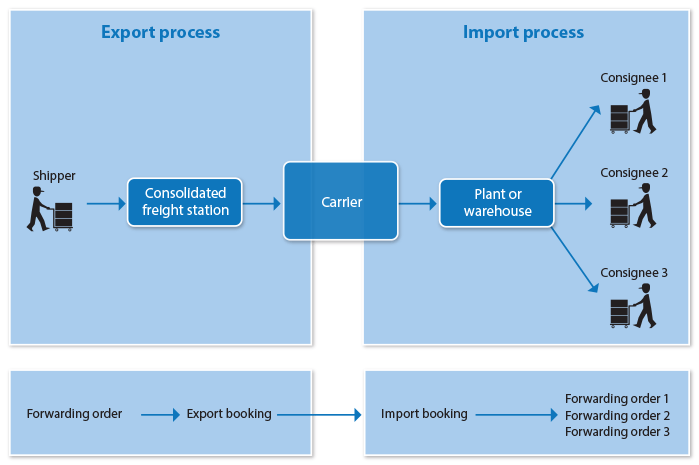
Figure 6
Shipper’s consolidation and de-consolidation of goods
Here the export user creates a single export forwarding order with a container item and sub-items for each package with different consignees. As soon as Shipped on Board or Uplift Confirmed is set on the export freight booking, import freight booking or import forwarding orders for each consignee are created.
The following incoterms are supported for a shipper’s consolidation scenario:
- Delivery Duty Paid (DDP) or Delivery Duty Unpaid (DDU)
- Delivered at Terminal (DAT) or Delivered at Place (DAP)
- Cost Insurance Freight (CIF) or Cost and Freight (CFR)
Note
An incoterm defines the responsibilities of sellers and buyers for the delivery of goods.
In shipper’s consolidation, an LSP charges FCL rates for pick-up and LCL rates for delivery.
In cases in which incoterms DDP, DDU, DAT, and DAP are applied, the export business unit creates one forwarding settlement order or one invoice for pickup, main leg, or delivery. The import business unit creates three forwarding settlement documents out of three forwarding orders for delivery to the export business unit.
When incoterm Cost, Insurance, and Freight (CIF) or Cost and Freight (CFR) are used, the export business unit creates one forwarding settlement order for pickup or main leg to shipper. The import business unit creates three invoices for delivery to the individual consignee out of import forwarding orders.
Consider this example: A leading freight forwarder was looking to map the shipper’s and buyer’s consolidation process to an existing SAP TM solution.
The freight forwarder had several requirements to meet. From ocean or air transport-based consolidation order consolidation, a separate printout of each house bill of lading (HBL) was required during the entire process. An end-to-end chronology of documents from export until import and POD were required. Customs processes needed to be mapped as a separate export declaration for each individual HBL. Security filing processes also needed to be mapped to the consolidation scenario. Process variations, including changes in consolidation plans and single versus multiple HBL scenarios, were necessary, and different pick-up services were required for each shipper.
We found that these requirements can only be managed by additional developments. There were also a lot of manual processes to consolidate or de-consolidate forwarding orders by assignment or de-assignment of freight units. It required additional training effort to transportation planners or logistics personnel. SAP TM also maps export documents to import documents via a status-based handover process (such as the departure or arrival of a vessel or a flight) Accommodating custom logic around these statuses requires further enhancement.
Note
While this functionality covers the basic form of shipper’s and buyer’s consolidation, the actual process of consolidation and de-consolidation is much more complex. To map it to SAP TM requires additional development effort. We think that the existing export and import mapping of shipping documents (forwarding order, freight booking or order) needs to be enhanced. Pricing (billing as well as invoicing) brings in additional complexity and requires more effort to map it to SAP TM.
Parcel Industry-Specific Functionalities
SAP TM 9.1 now handles all aspects of the parcel process, including:
- Picking and packing: determining the number of packages and creating a delivery based on transportation requirements or freight units
- Selecting shipping options: determining available carriers and comparing transportation services or costs, and manifesting
- Collecting parcel shipments for consolidation and communicating with the carrier: Executing and printing labels or manifests
- Loading and handing over to the carrier: monitoring execution and performing settlement
- Receiving or verifying invoices and payment
The process of picking and packing is done via ECC Delivery and Handling Unit (HU) management. Delivery is then transferred to SAP TM as delivery-based transportation requirements. For each delivery, a freight unit is created in SAP TM and the freight unit is assigned to the freight order for execution.
The freight unit represents Multi-Parcel shipment, for which the carrier or transportation service is determined.
After the freight unit is created, the direct shipment options (DSO) process is started. It selects a carrier based on the transportation network, determines freight agreements, and calculates charges for all valid ones. Then, it proposes the least expensive option.
It can also consider other constraints such as dates, dimensions, and trade lanes. A new tab, Direct Shipment Options, was introduced for this functionality. Pickup or delivery dates are determined based on transit times defined in the agreement. The freight unit is then assigned to the parcel freight order via the manifesting process.
All packages for the same consignee in a single freight unit are grouped as one shipment in the freight order. Shipment is created automatically for each freight unit assigned. Technically, waybill stock is used to model the shipment. External tracking IDs can also be assigned for each of these shipments.
Note that the parcel freight order does not contain a route based on stages. All parcels (freight units) are delivered from the shipper to the consignee based on the carrier route. For parcel freight orders, the shipment is used for charge calculation, so the calculation level is set to the item in the calculation profile.
Integration with Other SAP Modules
SAP TM 9.1 features enhanced integration with several other SAP modules. Enhanced integration includes the following:
- SAP TM-SAP EWM integration for warehouse planning and execution
- SAP TM-ERP integration for sales order scheduling and available-to-promise (ATP)
- SAP TM-CRM integration for opportunity to agreement creation
- SAP TM-SAP Global Trade Services (SAP GTS) integration for customs export and import processing
- SAP TM-SAP Environmental Health and Safety (EH&S) integration for dangerous goods compliance
SAP TM-SAP EWM Integration for Warehouse Planning and Execution
Integration of SAP TM 9.1 and SAP EWM 9.1 now supports both inbound and outbound good movements. Deliveries created in SAP ERP are transferred to SAP TM and SAP EWM. SAP TM does transportation planning on those deliveries and planning results are transferred to SAP EWM. In SAP EWM, transportation units are created and used for warehouse planning and execution. Confirmation of execution results (loading and quantity details) are directly sent to SAP TM.
SAP TM-SAP EWM integration now supports the following integrated warehousing and transportation processes:
- Order-based outbound processes
- Cancellation in order-based outbound processes
- Delivery-based outbound processes
The order-based outbound process starts with planning transportation in SAP TM based on sales orders in ERP. SAP TM sends delivery proposals to ERP. After deliveries are created, they are sent to SAP TM and SAP EWM. SAP TM creates a freight order. Based on it, SAP EWM creates a transportation unit and uses waves to pick up the goods. SAP ERP updates the deliveries, and SAP TM updates the freight order information for the freight cost settlement.
The cancellation in an order-based outbound process starts with a cancellation request from the carrier during picking of the goods. SAP EWM removes delivery orders from the transportation unit. SAP EWM sends a transportation unit (TU) cancellation to SAP TM, which further updates the freight order by removing assigned freight units.
The delivery-based outbound process starts with planning transportation based on outbound deliveries from SAP ERP. SAP TM creates a freight order. Based on it, SAP EWM creates a transportation unit and uses waves to pick up the goods. SAP ERP updates the deliveries, and SAP TM updates the freight order information for the freight cost settlement.
SAP TM-ERP Integration for Purchase or Sales Order Scheduling
Until SAP TM 9.0, purchase orders from ECC were moved to SAP TM as order-based transport requirements. SAP TM planning was done only on requested quantities. SAP TM 9.1 now allows transportation planning based on confirmed quantities. It means that freight units are created only after confirmed quantities are available in a purchase order in ECC.
In general, a confirmed quantity in a purchase order is populated only after an available-to-promise (ATP) check. It triggers acknowledgment confirmation control in the purchase order. This is now available in SAP TM so that you can see the schedule line as well as the acknowledgment.
It is now possible to use the handover location and dates in SAP TM as part of order-based transportation requirements. After freight units are generated based on these requirements, handover locations appear as part of stages as well. Note that stages can be created based on handover locations (such as Source > Handover Location or Handover Location > Destination). After the planning and creation of deliveries in SAP TM, handover location information can be sent back to SAP ERP. Inbound delivery can be updated with handover location information. Handover location is the physical location where goods are delivered by the vendor and is generally different from the receiving plant.
SAP TM 9.1 offers functionality to build stages based on the incoterm location. It has also added a new field – Shipping type in ECC Purchase order – Header and items, which is used to determine the mode of transport in order-based transportation requirements. SAP TM now also integrates with ECC based on delivery and credit check blocks available at the sales order or delivery level.
SAP TM-CRM Integration for Opportunity-to-Agreement Creation
SAP TM 9.1 now covers the entire opportunity-to-agreement process via close integration with SAP CRM (Figure 7). The process works as follows. As soon as a customer contacts a salesperson for an inquiry, a lead is created in SAP CRM. It moves to prospect, then to opportunity. Based on opportunity, a forwarding agreement quotation is created and sent to the customer. After the customer agrees to the quotation, a forwarding agreement is created in SAP TM.
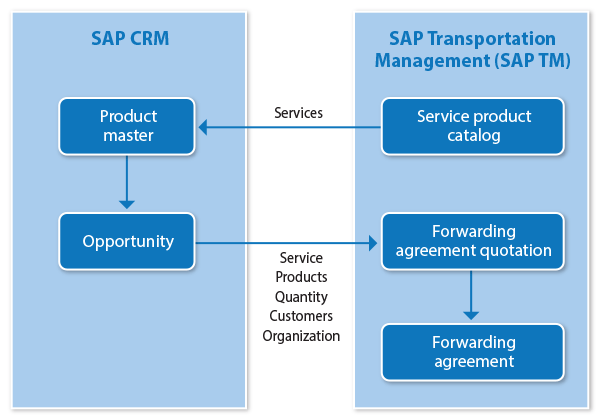
Figure 7
SAP TM-CRM integration
In terms of master data, a service product catalog created in SAP TM is now replicated to SAP CRM as a services product master. These services are included in an opportunity and then in subsequent documents such as the forwarding quotation or agreement.
Now, SAP CRM provides an embedded UI to access a variety of SAP TM transactions such as forwarding agreement quotation, forwarding agreement, and forwarding charges.
SAP TM-SAP GTS Integration for Customs Import Processing
SAP TM 9.1 has introduced functionality covering import declarations processed by LSPs. A freight forwarder can create an import declaration on behalf of shippers in import forwarding orders. Now, it’s possible to enter customs data and update customs statuses manually as well.
You can set customs handling as automatic in forwarding order type configuration. This setting enables SAP TM to check customs relevance beforehand and then generate import declarations at the port of destination. SAP TM has also introduced a checkbox in the forwarding order that specifies the import declaration to be done by an LSP. This setting can also be maintained at a specific business partner level.
SAP TM-SAP EH&S Integration for Dangerous Goods Compliance
SAP TM 9.1 supports the 1,000-point rule for transportation planning and execution of dangerous goods. According to this rule, the calculated value of hazardous goods to be transported for the same item may not exceed 1,000 points. If a quantity of hazardous goods exceeds the calculated value of 1,000 points, it is not allowed to be loaded into the same transportation unit.
SAP TM calculates these points at the document item or header and transportation stage level. The same rule is applied during freight unit building and planning of freight units via the optimizer.
With SAP TM 9.1, SAP has created a core platform for a supply chain execution network covering the end-to-end transportation process right from the shipper to the consignee, including all partners involved such as freight forwarders, export and import customs, and carriers.
Sanket Kulkarni
Sanket Kulkarni is a solution architect at Accenture Services Private Limited. He has about 15 years of SCM consulting experience in SAP implementation, rollout, and support projects. He has been associated with SAP Event Management for the last five years. He also has worked across a diverse range of SAP modules in the SCM suite, such as SAP Transportation Management (SAP TM), materials management (MM), SAP Advanced Planning and Optimization (APO), SAP Supply Network Planning (SNP), SAP Production Planning and Detailed Scheduling (PP/DS), Global Available-to-Promise (GATP), and Supply Network Collaboration (SNC) during his earlier assignments.
He has worked with clients in the discrete, consumer packaged goods (CPG), automotive, oil and gas, and semiconductor industries, as well as with transportation and carrier companies.
If you have comments about this article or publication, or would like to submit an article idea, please contact the editor.
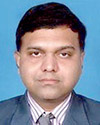
Rajesh Ray
Rajesh Ray currently leads the SAP SCM product area at IBM Global Business Services. He has worked with SAP SE and SAP India prior to joining IBM. He is the author of two books on ERP and retail supply chain published by McGraw-Hill, and has contributed more than 52 articles in 16 international journals. Rajesh is a frequent speaker at different SCM forums and is an honorary member of the CII Logistics Council, APICS India chapter and the SCOR Society.
You may contact the author at rajesray@in.ibm.com.
If you have comments about this article or publication, or would like to submit an article idea, please contact the editor.